
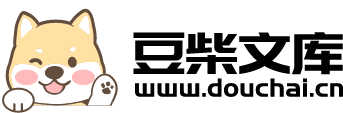
某反动式筒形高压内缸制造工艺研究.docx
快乐****蜜蜂
在线预览结束,喜欢就下载吧,查找使用更方便
相关资料
某反动式筒形高压内缸制造工艺研究.docx
某反动式筒形高压内缸制造工艺研究反动式筒形高压内缸是一种常用于航空发动机和涡轮机等高压液体或气体系统中的关键部件。它具有结构紧凑、高强度、高压力承载能力等优点,广泛应用于航空、航天、能源等行业。本文旨在研究反动式筒形高压内缸的制造工艺,通过对材料、加工工艺和参数优化等方面进行综述,以提供制造过程中的参考和指导。一、材料选择反动式筒形高压内缸所承受的高压力和温度要求材料具有良好的强度和耐热性能。一般选用具有较高熔点、高强度和耐腐蚀性的材料,如合金钢、不锈钢、钛合金等。材料的选择需要综合考虑内部应力分布、工艺
反动式筒形高压内缸加工工艺分析与探究.docx
反动式筒形高压内缸加工工艺分析与探究反动式筒形高压内缸是一种广泛应用于汽车发动机的重要零部件,其制造工艺的优劣直接影响着汽车发动机的性能和可靠性。本文将从工艺分析和探究的角度对反动式筒形高压内缸的加工工艺进行研究。首先,根据反动式筒形高压内缸的结构特点和工艺要求,对其加工工艺进行分析。筒形高压内缸一般由铸钢材料制造,其内外表面应具备高度精度和良好的尺寸一致性。加工工艺主要包括下料、车削、磨削和加工表面处理等步骤。在下料过程中,需要确保材料的质量和尺寸合格,以保证加工后的内缸的质量。车削和磨削是内缸加工的主
100 MW级反动式高压内缸制造工艺流程探究.pptx
汇报人:/目录01反动式高压内缸的定义反动式高压内缸的作用反动式高压内缸的应用场景02制造前的准备材料选择与处理零件加工与组装热处理与表面处理质量检测与控制03铸造技术焊接技术机械加工技术无损检测技术04材料处理难点与对策加工精度控制难点与对策热处理变形控制难点与对策无损检测技术难点与对策05提高材料利用率降低制造成本提高生产效率提升产品质量06智能化制造技术的应用新材料的应用与发展绿色制造与环保要求国际化标准与认证汇报人:
汽轮机高压内缸的制造工艺研究.pptx
添加副标题目录PART01汽轮机高压内缸的制造工艺简介汽轮机高压内缸的制造工艺流程汽轮机高压内缸的制造工艺重要性PART02高压内缸材料的要求高压内缸材料的种类高压内缸材料的选择依据PART03高压内缸的铸造工艺高压内缸的热处理工艺高压内缸的机械加工工艺PART04高压内缸的质量检测方法高压内缸的质量控制标准高压内缸的质量控制措施PART05制造工艺的自动化和智能化发展制造工艺的环境友好性发展制造工艺的创新发展PART06高压内缸在汽轮机中的应用现状高压内缸在汽轮机中的未来应用前景高压内缸的应用对汽轮机发
50MW等级光热发电高转速反动式高压缸制造技术研究.docx
50MW等级光热发电高转速反动式高压缸制造技术研究50MW等级光热发电高转速反动式高压缸制造技术研究摘要:光热发电是一种利用太阳能将光能转化为热能,再将热能转化为电能的一种可持续发展能源技术。在光热发电系统中,高压缸是关键设备之一,其制造技术对于系统性能和运行效率具有重要影响。本论文以50MW等级光热发电系统中的高压缸为研究对象,从材料选择、制造工艺、设计与模拟等方面进行探究,目的是提高光热发电系统的发电效率和可靠性。第一部分:引言光热发电作为一种可再生的能源技术,有着广阔的应用前景。其中,高压缸作为光热