
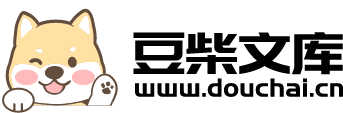
齿轮损坏原因.docx
快乐****蜜蜂
亲,该文档总共11页,到这已经超出免费预览范围,如果喜欢就直接下载吧~
相关资料
齿轮损坏原因.docx
齿轮损坏的主要原因大致分为:磨损;起麻点、剥落、渗碳层碎裂;疲劳;撞击;波纹、起棱和冷变形。大多数齿轮的损坏是因为齿轮载荷过大,或者因不正确的换档或操纵离合器引起撞击或震动载荷。如果一个齿轮内部有缺陷,只有通过金相检查才能确定。磨损磨损是表面材料从齿轮上的去除。它可能是缓慢的,如划伤,或是迅速的,如擦伤。磨损有三种型式:粘附磨损—由金属与金属接触,并且表面粘接到一起而后撕离所造成.原因可能是润滑油不足,或齿轮没有正确啮合。磨料磨损―由外界颗粒,如灰尘和砂粒造成。腐蚀磨损―由污染的润滑油或者添加剂产生的对齿
机床齿轮损坏原因及解决策略分析.docx
机床齿轮损坏原因及解决策略分析齿轮是机床中最重要的一个部件,也是最受保护的一个部件之一。但在实践中齿轮常常因为各种各样的原因而损坏,本文就机床齿轮的损坏原因给出具体的分析,并针对这些原因给出解决的策略。机床齿轮在整个机床流程过程中起到非常重要的作用,尤其对于机床进行金属切削来说,具有精度高、结构紧凑、转动链复杂、自动化程度高等特点,常常因为各种各样的原因造成机床齿轮的损坏。大多数机床齿轮损坏的原因是因为齿轮的负荷过大,或者由于操作者的非正常操作而引起的,本文讨论的机床齿轮损坏原因不包括人为因素,具体机床齿
废料夹送辊齿轮电机损坏原因分析及改进.docx
废料夹送辊齿轮电机损坏原因分析及改进废料夹送辊齿轮电机损坏原因分析及改进摘要:本文以废料夹送辊齿轮电机损坏为研究对象,通过分析损坏原因,提出了相应的改进措施。齿轮电机是废料夹送机主要的驱动装置,其正常工作对于整个生产线的稳定运行至关重要。然而,在实际生产过程中,废料夹送辊齿轮电机存在损坏频繁的问题。本研究通过对废料夹送辊齿轮电机的工作原理和结构特点进行分析,从机械设计、使用维护以及运行参数等多个方面探讨了齿轮电机损坏的原因,并提出了相应的改进措施,为废料夹送辊齿轮电机的安全运行提供参考。关键词:废料夹送机
核电盘车装置相位齿轮损坏原因分析及改进.docx
核电盘车装置相位齿轮损坏原因分析及改进导言核能是一种清洁的、长期、可靠和安全的能源,其中核电站是核能发电的主要设施。由于其关键性和高风险性,核电站的安全性是非常重要的。核电盘车装置是核电站中的重要设备之一,该装置的正常运行对于保障核电站运行的安全性有着至关重要的作用。然而,该设备在运行中存在诸多问题,其中相位齿轮损坏问题一直是该装置的一大难题。本文将围绕核电盘车装置中相位齿轮损坏的原因分析及改进进行阐述,希望能为该装置的改进提供参考。一、核电盘车装置简介核电盘车装置是一种核电站用来装卸燃料棒、燃料组件和燃
煤矿机械传动齿轮损坏原因及解决方法.docx
煤矿机械传动齿轮损坏原因及解决方法-1--4-煤矿机械传动齿轮损坏原因及解决方法随着时代的发展我国煤矿工作已经迈入了先进的机械时代。但是由于行业的特殊性煤矿工作的环境比较恶劣由于长时间在阴暗潮湿的条件下工作很多机械设备经常发生故障从而引发煤矿事故。其中比较频繁发生的就是机械传动齿轮发生损坏导致设备无法正常运转本文将以此为切入点寻求解决齿轮损坏的原因并且有针对性的提出一些方案措施。传动齿轮的优点颇多例如具备较强的承载能力较高的精准度以及恒功率转动的优势所以备受煤矿企业的青睐。但煤炭生产不但工作环境