
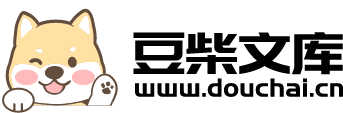
加氢合成邻氨基苯甲醛的工艺研究.docx
骑着****猪猪
在线预览结束,喜欢就下载吧,查找使用更方便
相关资料
加氢合成邻氨基苯甲醛的工艺研究.docx
加氢合成邻氨基苯甲醛的工艺研究近年来,邻氨基苯甲醛作为一种重要的有机化学品,广泛应用于颜料、染料、医药、农药等领域。其合成方法种类繁多,其中加氢合成法是一种较为常用的方法。本文将围绕加氢合成邻氨基苯甲醛的工艺研究展开,并从催化剂选择、反应条件、工艺优化等方面进行探讨。一、催化剂选择催化剂是加氢合成邻氨基苯甲醛的关键因素之一。在过去的研究中,常用的催化剂有铜催化剂、镍催化剂、铂催化剂等。铜催化剂具有活性高、价格低等优点,但其不易把握反应温度,且难以控制产品纯度,故现不常用。镍催化剂具有选择性较好、易于操作等
邻氨基苯磺酸合成工艺改进.docx
邻氨基苯磺酸合成工艺改进邻氨基苯磺酸是一种重要的有机合成中间体,广泛应用于医药、染料、涂料等领域。本文旨在改进邻氨基苯磺酸的合成工艺,提高产率和产品纯度,减少副产物产生,并降低生产成本。一、目前合成工艺存在的问题目前合成邻氨基苯磺酸的常用方法是亚硝基苯与苯胺在酸性条件下反应生成邻氨基苯磺酸。然而,该合成工艺存在多个问题:1.低产率:传统合成工艺中,底物苯胺和亚硝基苯反应生成邻氨基苯磺酸的产率较低,一部分底物无法完全转化为目标产物,导致产率低下。2.副产物多:该反应产生的副产物有苯胺二硝基化物、氮氧化合物等
邻硝基苯甲醛合成工艺的改进.docx
邻硝基苯甲醛合成工艺的改进邻硝基苯甲醛(2-nitrobenzaldehyde)是一种重要的化工中间体和有机合成原料,广泛应用于医药、染料、农药和精细化工等领域。其合成工艺及反应条件的优化对于提高产率、提高纯度和减少废物排放具有重要意义。本文将就邻硝基苯甲醛合成工艺进行改进的若干方面进行探讨。一、反应路线优化邻硝基苯甲醛的合成可通过对硝基苯(nitrobenzene)和甲醛(formaldehyde)的反应得到。现有的常规方法主要包括氧化还原反应、硝化还原反应等。然而,这些方法不仅反应条件较为严苛,而且废
邻硝基苯甲醛合成工艺改进.docx
邻硝基苯甲醛合成工艺改进邻硝基苯甲醛合成工艺改进摘要:邻硝基苯甲醛是一种重要的有机化工原料,在合成某些药物和染料方面具有广泛的应用。然而,传统的合成工艺存在高温高压、废料多、反应效率低等问题。针对这些问题,本文对邻硝基苯甲醛的合成工艺进行了改进,并采用新的工艺方法,通过控制反应的温度和催化剂的选择,提高了合成的反应效率和产率,并减少了废料的生成。一、引言邻硝基苯甲醛是一种重要的有机化工原料,广泛应用于医药、染料和化妆品等领域。传统的合成方法主要是通过硝酸与甲苯进行反应,但该方法存在一些问题,如高温高压、废
邻苯二甲醛消毒剂合成工艺研究.doc
目录TOC\o"1-3"\h\zHYPERLINK\l"_Toc257275115"前言PAGEREF_Toc257275115\h1HYPERLINK\l"_Toc257275116"1城市现状PAGEREF_Toc257275116\h2HYPERLINK\l"_Toc257275117"1.1自然状况PAGEREF_Toc257275117\h2HYPERLINK\l"_Toc257275118"1.2社会经济发展现状PAGEREF_Toc2572751