
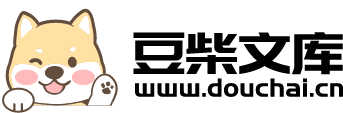
基于HyperStudy平台的材料参数优化.docx
快乐****蜜蜂
在线预览结束,喜欢就下载吧,查找使用更方便
相关资料
基于HyperStudy平台的材料参数优化.docx
基于HyperStudy平台的材料参数优化基于HyperStudy平台的材料参数优化杨萌华为技术有限公司深圳518057摘要:针对当前仿真工作中仿真结果与实际测试结果存在一定差异的问题,本文应用HyperStudy软件的参数优化功能,对镁合金板条的材料参数进行了优化。确定优化方法后在三点弯折工况下对手机复杂结构件材料参数进行优化,并将优化后材料参数在结构件不同工况下进行了验证。研究结果表明:通过HyperStudy的材料参数优化方法,获得了更适用于仿真的材料参数,从而有效的解决了仿真结果和实际测试结果之间
基于HyperStudy平台的材料参数优化(完整资料).doc
基于HyperStudy平台的材料参数优化(完整资料)(可以直接使用,可编辑优秀版资料,欢迎下载)基于HyperStudy平台的材料参数优化基于HyperStudy平台的材料参数优化杨萌华为技术有限公司深圳518057摘要:针对当前仿真工作中仿真结果与实际测试结果存在一定差异的问题,本文应用HyperStudy软件的参数优化功能,对镁合金板条的材料参数进行了优化.确定优化方法后在三点弯折工况下对手机复杂结构件材料参数进行优化,并将优化后材料参数在结构件不同工况下进行了验证.研究结果表明:通过HyperSt
基于HyperStudy平台的材料参数优化【实用文档】doc.doc
基于HyperStudy平台的材料参数优化【实用文档】doc文档可直接使用可编辑,欢迎下载基于HyperStudy平台的材料参数优化基于HyperStudy平台的材料参数优化杨萌华为技术有限公司深圳518057摘要:针对当前仿真工作中仿真结果与实际测试结果存在一定差异的问题,本文应用HyperStudy软件的参数优化功能,对镁合金板条的材料参数进行了优化.确定优化方法后在三点弯折工况下对手机复杂结构件材料参数进行优化,并将优化后材料参数在结构件不同工况下进行了验证.研究结果表明:通过HyperStudy的
基于HyperStudy和隐式参数化模型的A柱综合性能优化.docx
更多资料请登录基于HyperStudy和隐式参数化模型的A柱综合性能优化张继游1,2,彭鸿1,2,门永新1,2,赵福全1,21.吉利汽车研究院,杭州,311228;2.浙江省安全控制技术重点实验室,杭州,311228摘要:本文在HyperStudy优化平台的基础上,采用参数化技术和优化技术,集成了OptiStruct等求解器,对某车型A柱的综合性能(刚度、屈曲和压溃性能)进行优化,最后获得了满足设计指标并且单位长度质量最小的设计方案。关键字:HyperStudy,OptiStruct,隐式参数化模型,A柱
HyperStudy平台下结构抗震优化设计方法研究.docx
HyperStudy平台下结构抗震优化设计方法研究为题目,写不少于1200的论文AbstractInthisstudy,astructuralearthquake-resistantoptimizationdesignmethodbasedonHyperStudyplatformwasproposed.Bycombiningthefiniteelementanalysisandtheoptimizationalgorithm,theobjectiveofminimizingthedisplacemento