
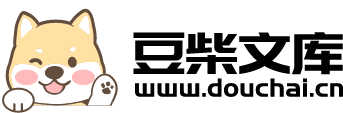
AZ91镁合金等径角挤压前后组织性能分析.docx
快乐****蜜蜂
亲,该文档总共15页,到这已经超出免费预览范围,如果喜欢就直接下载吧~
相关资料
AZ91镁合金等径角挤压前后组织性能分析.docx
毕业设计(论文)开题报告题目:AZ91镁合金等径角挤压前后组织性能分析学院:机械工程学院专业:材料成型及控制工程学生姓名:刘集思学号:201102050119指导老师:吴安如2015年3月20日毕业设计(论文)开题报告文献综述0引言镁基复合材料具有密度小、比强度和比刚度高、导热和导电性好,极好的减震性能、优良的阻尼性和易于加工成形和回收等优点,电磁屏蔽性、越来越广泛地应用于航空航天、汽车、3C电子、环保等领域。目前关于镁基复合材料的研究工作主要集中于材料组成、制备工艺和材料组织及性能等方面。等径道角挤压(
AZ91镁合金挤压组织与性能的试验研究.docx
AZ91镁合金挤压组织与性能的试验研究摘要:在本文中,我们对AZ91镁合金进行了挤压实验,分析了材料的组织和力学性能。我们使用传统的金属材料测试方法对样品进行了测试,采用了光学显微镜和电子显微镜对样品的组织进行分析。结果表明,AZ91镁合金具有明显的细晶化效应,在高温下具有良好的塑性和变形能力,而且在高压下表现出了较强的硬度和强度。关键词:AZ91镁合金,挤压,组织,性能引言:镁合金因其低密度、高比强度和高可回收性等优点而在工业生产中得到了广泛应用。然而,由于其在高温和高压下的易氧化性和低塑性,对其进行加
工艺参数对AZ91镁合金挤压组织及性能的影响.docx
工艺参数对AZ91镁合金挤压组织及性能的影响AZ91镁合金是一种优良的轻质材料,它具有优异的机械性能和耐腐蚀性能,广泛应用于航空、汽车、电子、家具等领域。挤压是常见的加工方法之一,它可以提高材料的强度和硬度,改善材料的耐磨性和表面质量。然而,挤压过程中的工艺参数对材料的结构和性能有着重要的影响,因此本文将探讨工艺参数对AZ91镁合金挤压组织及性能的影响。1.挤压温度挤压温度是影响AZ91镁合金组织和性能的关键因素之一。当温度太高时,大量的气孔、金属间化合物等会出现在挤压体中,从而导致组织不均匀,降低了材料
ZK60镁合金等径角挤压研究.docx
ZK60镁合金等径角挤压研究摘要:镁合金是一种轻质高强度的金属材料,被广泛应用于航空、汽车等领域。在当前模具技术水平下,等径角挤压成为一种有效的镁合金加工方法。本文研究了ZK60镁合金等径角挤压的力学特性、金相结构和表面微观形貌。分析结果表明,等径角挤压可以改善ZK60镁合金的力学性能和表面质量,提高其应用价值。关键词:ZK60镁合金、等径角挤压、力学性能、金相结构、表面微观形貌Abstract:Magnesiumalloyisalightweightandhigh-strengthmetalmateri
ZK60镁合金等径角挤压研究的综述报告.docx
ZK60镁合金等径角挤压研究的综述报告ZK60镁合金是一种优秀的轻质高强度合金,广泛应用于航空、航天、汽车、电子和医疗等领域。等径角挤压技术是一种有效的制备高品质ZK60镁合金材料的方法。本文将对ZK60镁合金等径角挤压研究进行综述,重点介绍其工艺、显微组织和力学性能等方面的研究进展。一、等径角挤压工艺等径角挤压技术从近几十年来发展迅速。该技术通过在挤压过程中调节模具径角的大小,在保持断面积不变的前提下使材料流动路径改变,从而实现均匀变形和细化晶粒的目标。其主要研究方向包括挤压力、模具形状和加工参数等关键