
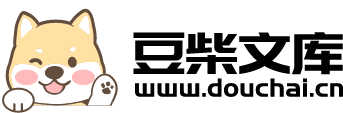
裂纹对弧齿锥齿轮接触应力影响研究.docx
快乐****蜜蜂
在线预览结束,喜欢就下载吧,查找使用更方便
相关资料
裂纹对弧齿锥齿轮接触应力影响研究.docx
裂纹对弧齿锥齿轮接触应力影响研究摘要本文研究了裂纹对弧齿锥齿轮接触应力的影响,通过有限元分析和实验测量,得出了裂纹在弧齿锥齿轮上的不同位置和不同尺寸对接触应力的影响。研究表明,裂纹会导致弧齿锥齿轮的强度降低,从而影响齿轮的可靠性和寿命。因此,在设计和使用弧齿锥齿轮时,应注意裂纹的形成和扩展,及时采取相应措施,保证齿轮的正常运行。关键词:裂纹;弧齿锥齿轮;接触应力;有限元分析;实验测量引言弧齿锥齿轮是一种常用的传动元件,广泛应用于机械、航空航天、汽车等领域。在弧齿锥齿轮的设计和使用过程中,裂纹是一个重要的问
等高齿弧齿锥齿轮加工工艺研究.docx
等高齿弧齿锥齿轮加工工艺研究摘要:本文主要探讨了等高齿弧齿锥齿轮的加工工艺研究问题。随着机械制造行业的不断发展,精度和耐用性越来越成为消费者选择产品的标准之一。因此,在锥齿轮设计和加工过程中,精度的控制和优化是至关重要的。本文介绍了锥齿轮的相关知识以及加工工艺的流程和方法,重点讨论了等高齿弧齿锥齿轮的加工技术和精度的控制,最后提出了一些未来发展的方向。关键词:锥齿轮;等高齿弧齿;精度;加工工艺研究一、引言锥齿轮是机械传动中常用的零部件,它具有传动力矩大、速度比稳定、噪声小等优点,广泛应用于重型机械、汽车、
等高齿弧齿锥齿轮加工工艺研究.docx
等高齿弧齿锥齿轮加工工艺研究等高齿弧齿锥齿轮加工工艺研究摘要:等高齿弧齿锥齿轮是一种常见的传动元件,在机械领域中广泛应用。本文以等高齿弧齿锥齿轮的加工工艺为研究对象,探讨了其加工方法、加工工艺及加工质量控制等方面的问题。结果表明,合理选择加工方法和工艺参数,严格控制加工精度,能够提高等高齿弧齿锥齿轮的加工质量和使用性能。关键词:等高齿弧齿锥齿轮;加工工艺;加工精度;加工质量1.绪论等高齿弧齿锥齿轮是一种常见的齿轮传动元件,具有结构简单、传动效率高等特点,在汽车、机床、飞机等机械设备中被广泛应用。其加工工艺
点蚀对弧齿锥齿轮传动误差影响的研究.docx
点蚀对弧齿锥齿轮传动误差影响的研究标题:点蚀对弧齿锥齿轮传动误差影响的研究摘要:随着工业技术的不断发展,弧齿锥齿轮传动作为重要的机械传动装置在各个领域得到广泛应用。然而,在长时间高速运转中,由于各种复杂因素的综合作用,锥齿轮传动常常会出现点蚀现象,导致传动精度下降、传动效率降低甚至传动失效。本文通过对点蚀对弧齿锥齿轮传动误差影响的研究,分析了点蚀对弧齿锥齿轮传动性能的影响机理,提出了相应的解决方案,旨在为弧齿锥齿轮传动的优化设计与可靠运行提供参考。关键词:点蚀;弧齿锥齿轮;传动误差;影响机理;解决方案1.
直齿锥齿轮接触应力分布规律研究.docx
直齿锥齿轮接触应力分布规律研究一、引言直齿锥齿轮是常见的传动元件,广泛应用于高负荷、高速和高精度的工程领域。在设计和制造过程中,了解齿轮接触应力分布规律对于保证齿轮传动系统的可靠性和寿命具有重要作用。本文将探讨直齿锥齿轮接触应力分布规律的研究进展和应用。二、直齿锥齿轮接触应力分析方法直齿锥齿轮的接触应力分析一般采用有限元方法和解析方法两种途径。有限元方法是将齿轮分解为有限的单元,将节点之间的应力、位移等参数用有限元方程表示,通过计算单元之间的相互作用,获得系统的应力分布规律。该方法优点是可以考虑复杂的几何