
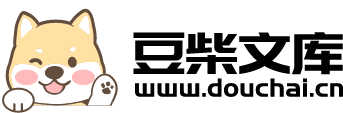
聚乙烯管材热熔对接焊接接头无损检测技术进展.docx
快乐****蜜蜂
在线预览结束,喜欢就下载吧,查找使用更方便
相关资料
聚乙烯管材热熔对接焊接接头无损检测技术进展.docx
聚乙烯管材热熔对接焊接接头无损检测技术进展聚乙烯管材热熔对接焊接接头无损检测技术进展摘要:聚乙烯管材在输送液体、气体和固体粉末等方面具有广泛的应用。然而,热熔对接焊接接头在制造过程中容易产生一些缺陷,如气孔、裂纹等,严重影响管道的性能和可靠性。因此,应用无损检测技术对热熔对接焊接接头进行检测成为必要的手段。本文综述了聚乙烯管材热熔对接焊接接头无损检测技术的最新进展,包括超声波检测、射线检测、红外热像检测、涡流检测以及激光扫描等方法,分析了各种方法的原理和优缺点,并对未来的研究方向进行了展望。关键词:聚乙烯
钢筋焊接接头无损检测技术.docx
钢筋焊接接头无损检测技术超声波检测法钢筋是一种带肋棒状材料。钢筋气压焊接头的缺陷一般呈平面状存在于压焊面上,而且探伤工作只能在施工现场进行。因此,采用脉冲波双探头反射法在钢筋纵肋上进行探查是切实可行的。检测原理当发射探头对接头射入超声波时,不完全接合部分对入射波进行反射,此反射波又被接收探头接收。由于接头抗拉强度与反射波强弱有很好的相关关系,故可以利用反射波的强弱来推断接头的抗拉强度,从而确保接头是否合格。检测方法使用气压焊专用简易探伤仪的检测步骤:纵筋的处理:用纱布或磨光机把接头徽粗两侧1~150mm范
红外热波无损检测技术及其进展.docx
红外热波无损检测技术及其进展摘要:综述了红外热波无损检测技术的基本原理、技术特点,给出了一些典型的应用试验结果,介绍了国内外相应研究的发展状况和进展。关键词:红外热波;无损检测;热波检测红外热波无损检测技术(简称热波检测)是一门跨学科的技术。它的研究和应用,对提高航空航天器,多种军、民用工业设备的安全可靠性具有重要意义。美国多家大公司(如GE、GM、福特、洛克西德和西屋等)及政府机构(如NASA、FAA、空军、海军)等已经在广泛应用和推广该技术。2003年9月该项技术的应用研究也列入了我国国家863高科技
红外热波无损检测技术及其进展.docx
红外热波无损检测技术及其进展摘要:综述了红外热波无损检测技术的基本原理、技术特点,给出了一些典型的应用试验结果,介绍了国内外相应研究的发展状况和进展。关键词:红外热波;无损检测;热波检测红外热波无损检测技术(简称热波检测)是一门跨学科的技术。它的研究和应用,对提高航空航天器,多种军、民用工业设备的安全可靠性具有重要意义。美国多家大公司(如GE、GM、福特、洛克西德和西屋等)及政府机构(如NASA、FAA、空军、海军)等已经在广泛应用和推广该技术。2003年9月该项技术的应用研究也列入了我国国家863高科技
焊接对接接头磁粉检测工艺.doc
1.总则1.1合用范围本工艺合用于承压设备焊接对接接头旳磁粉检测。1.2编制根据(1)委托书和承压设备设计、制造资料。(2)JB/T4730.4-第四部分:磁粉检测。1.3检测人员符合JB/T4730.4-旳第3.1条规定。2.被检工件受检焊接对接接头表面不得有油脂、铁锈、氧化皮或其他粘附磁粉旳物质。表面打磨圆滑过渡、露出金属光泽。3.设备和器材3.1设备:交叉磁轭探伤仪或磁轭式探伤仪,质量符合JB/T4730.4-旳3.3条规定。3.2器材:黑磁粉、水磁悬液,质量符合JB/T4730.4-旳3.4条规定