
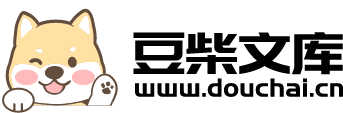
萃取精馏分离苯环己烷共沸体系模拟与优化.docx
快乐****蜜蜂
在线预览结束,喜欢就下载吧,查找使用更方便
相关资料
萃取精馏分离苯环己烷共沸体系模拟与优化.docx
萃取精馏分离苯环己烷共沸体系模拟与优化萃取精馏分离苯环己烷共沸体系模拟与优化论文一、引言苯和环己烷是广泛存在于化工行业中的基础化学品,两者组成的共沸体系在现实工业生产中也经常遇到。为了实现苯和环己烷的分离和提取,就需要运用化学工程学中的方法,对其进行精细的分离,以达到工业生产的要求。萃取精馏分离是一种被广泛应用的化工分离技术。本文旨在运用经典的化学工程学原理,对苯和环己烷的共沸体系进行模拟和优化,提高提取和分离的效率,降低成本。二、共沸体系模拟1.实验环境为了模拟和优化苯和环己烷的共沸体系,我们需要使用A
萃取精馏分离甲苯-乙醇共沸体系的模拟与优化.docx
萃取精馏分离甲苯-乙醇共沸体系的模拟与优化摘要:本文以甲苯-乙醇共沸体系为研究对象,采用AspenPlus软件模拟该体系的萃取精馏分离过程,并对该过程进行优化。首先,根据实验数据,建立了热力学模型和动力学模型,并对模型进行了验证。随后,通过改变工艺参数,如进料速率、塔板数、塔径等,对分离效果进行了优化。最终,得到了适合该体系的最佳工艺参数,进料速率为200kg/h、塔板数为30板、塔径为60cm。关键词:甲苯-乙醇共沸体系;AspenPlus;模拟;优化引言:甲苯-乙醇共沸体系是一种特殊的混合物体系,其组
萃取精馏分离异丙醇-水共沸体系的模拟与优化.docx
萃取精馏分离异丙醇-水共沸体系的模拟与优化引言异丙醇是常见的工业有机溶剂之一,广泛应用于溶剂浸提、常压蒸馏、分馏和萃取等工业过程中。与水混合后,异丙醇-水体系具有共沸现象,其中异丙醇和水成为了两种相对等概率存在的共沸体系,因此在实际应用中难以分离。而异丙醇和水的萃取精馏分离技术正是针对这种共沸现象所设计的一种方法。由于其结构复杂和过程的多变性,萃取精馏分离异丙醇-水共沸体系一直是研究的热点之一。本文旨在对异丙醇-水共沸体系的萃取精馏分离进行模拟和优化。实验方法1.萃取装置采用的萃取装置为结构为圆柱形的萃取
丙酮-氯仿共沸体系萃取精馏过程模拟与优化.docx
丙酮-氯仿共沸体系萃取精馏过程模拟与优化摘要:本研究以丙酮和氯仿的共沸体系为研究对象,利用化工领域中常用的萃取和精馏技术,对其进行模拟和优化研究。通过建立数学模型,探究了操作参数(包括温度、压力、物料比等)对萃取和精馏过程的影响,并且对处理后的产品进行了分析,验证了优化结果的可行性和有效性。关键词:丙酮;氯仿;共沸体系;萃取;精馏;模拟;优化1.研究背景丙酮和氯仿的共沸体系在化工行业中被广泛应用。一般情况下,它们是通过萃取和精馏技术进行分离和提纯的。因此,研究共沸体系萃取精馏过程的模拟和优化,对化工领域的
连续萃取精馏分离环己烯-环己烷的模拟与优化.docx
连续萃取精馏分离环己烯-环己烷的模拟与优化连续萃取精馏分离环己烯-环己烷的模拟与优化摘要:本文针对环己烯和环己烷的分离问题,通过连续萃取精馏的方法进行模拟和优化。首先,利用Matlab软件建立了环己烯-环己烷的物性参数模型,然后基于该模型对连续萃取精馏过程进行了模拟。最后,通过对操作条件的调整,得到了最佳的分离效果。实验结果表明,连续萃取精馏是一种有效的分离方法,可以实现环己烯和环己烷的高效分离。关键词:连续萃取精馏;环己烯;环己烷;模拟;优化1.引言环己烯和环己烷是常用的有机溶剂,广泛用于化工、医药等领