
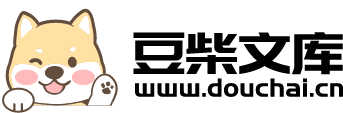
热处理工艺对铝硅-聚苯酯涂层可磨耗性能的影响.docx
快乐****蜜蜂
在线预览结束,喜欢就下载吧,查找使用更方便
相关资料
热处理工艺对铝硅-聚苯酯涂层可磨耗性能的影响.docx
热处理工艺对铝硅-聚苯酯涂层可磨耗性能的影响摘要:本论文对热处理工艺对铝硅-聚苯酯涂层可磨耗性能的影响进行研究。通过对样品进行热处理,分别在600℃、700℃、800℃三种温度下处理,然后采用球盘磨削法对处理前后的样品进行测试。结果表明,热处理工艺对铝硅-聚苯酯涂层的可磨耗性能有着一定的影响。温度为600℃时,处理后的样品的可磨耗性能有所提高;当温度升高至700℃和800℃时,磨损量反而增加。因此,为了在铝硅-聚苯酯涂层中获得更好的可磨耗性能,在热处理过程中需要考虑合适的温度。关键词:铝硅-聚苯酯涂层;热
大气等离子喷涂铝硅-聚苯酯涂层的工艺及性能研究.docx
大气等离子喷涂铝硅-聚苯酯涂层的工艺及性能研究摘要:本文研究了大气等离子喷涂铝硅-聚苯酯涂层的工艺与性能,主要对涂层的化学成分、涂层的晶体结构、涂层的机械性能以及涂层的耐磨性、耐腐蚀性等方面进行了分析和探讨。结果表明,大气等离子喷涂铝硅-聚苯酯涂层具有良好的机械性能和耐磨性、耐腐蚀性,可以应用于航空航天、船舶、机械、汽车等行业中的高耐磨、高耐腐蚀的涂层。关键词:大气等离子喷涂;铝硅;聚苯酯;涂层;机械性能;耐磨性;耐腐蚀性一、引言在现代工业中,对于增强材料的性能,涂层技术是一种常用的手段,特别是对于金属材
铜铝聚苯酯涂层性能研究.pptx
,aclicktounlimitedpossibilities目录PartOne铜铝聚苯酯涂层的组成成分铜铝聚苯酯涂层的物理性质铜铝聚苯酯涂层的化学性质PartTwo制备方法制备参数制备过程中的注意事项PartThree建筑领域汽车领域航空航天领域其他领域PartFour耐候性能测试耐腐蚀性能测试耐磨性能测试其他性能测试与评估PartFive发展趋势技术难题与挑战未来展望THANKS
不同造孔剂含量的铝硅聚苯酯粉末制备涂层性能研究.docx
不同造孔剂含量的铝硅聚苯酯粉末制备涂层性能研究【摘要】本研究通过制备不同含量造孔剂的铝硅聚苯酯粉末,成功制备出涂层材料,并对其性能进行研究。实验结果表明,适量添加造孔剂可以有效提高涂层的吸湿性和呼吸性,但同时也会降低其耐腐蚀性能。该研究为铝硅聚苯酯涂层材料的开发提供了有益的参考。【关键词】铝硅聚苯酯;造孔剂;涂层;性能研究【引言】铝硅聚苯酯是一种优良的高分子材料,具有良好的物理性质和化学稳定性,在制备涂层材料方面有着广泛的应用。随着涂层技术的不断发展,对涂层材料的要求也越来越高。除了常规的性能指标,如耐腐
铝硅聚苯酯封严涂层切向载荷作用下应力分布的有限元分析.docx
铝硅聚苯酯封严涂层切向载荷作用下应力分布的有限元分析一、引言铝硅聚苯酯是一种高性能聚合物,具有良好的机械强度、耐热性、防腐蚀性能等一系列优点。因其具有良好的保护性能,被广泛应用于油气、航空、船舶等领域的密封、粘合和防腐蚀。而切向载荷作用下的应力分布,则是其在设计和生产过程中需要优先考虑的问题。本文将从有限元分析的角度出发,对铝硅聚苯酯封严涂层切向载荷作用下的应力分布进行分析和研究。二、研究方法和假设条件1.分析方法:有限元分析法;2.研究对象:铝硅聚苯酯封严涂层;3.材料参数:密度ρ=1.45×10³kg