
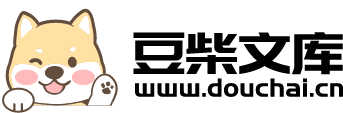
复合结构界面粘接质量的超声衰减法研究.docx
快乐****蜜蜂
在线预览结束,喜欢就下载吧,查找使用更方便
相关资料
复合结构界面粘接质量的超声衰减法研究.docx
复合结构界面粘接质量的超声衰减法研究摘要复合结构在航空、汽车、能源等领域具有广泛的应用。然而,复合结构的界面粘接质量是影响复合材料结构性能的关键因素之一。本文研究了利用超声衰减法评估复合结构界面粘接质量的方法。通过实验验证和文献综述,发现超声衰减法具有非破坏性、高灵敏度、高重复性等优点,能够有效地评估复合结构界面粘接质量。同时,本文还讨论了超声衰减法在界面粘接研究中的应用前景和存在的问题。关键词:复合结构;界面粘接;超声衰减法;评估方法1.引言复合材料结构近年来在航空、汽车、能源等领域得到了广泛应用,因为
多界面粘接构件粘接质量的超声检测与识别.docx
多界面粘接构件粘接质量的超声检测与识别多界面粘接构件粘接质量的超声检测与识别摘要:随着工业化的发展,多界面粘接构件在航空航天、汽车制造、建筑工程等领域得到广泛应用。粘接界面质量是影响粘接构件性能和寿命的关键因素之一。因此,粘接界面质量的检测与识别对于保证粘接构件的可靠性至关重要。本文基于超声技术,研究了多界面粘接构件粘接质量的非破坏检测与识别方法。关键词:超声检测;多界面粘接构件;粘接质量;非破坏检测;识别方法1.引言多界面粘接构件是由两个或多个部件通过胶粘剂黏结在一起的复合材料构件。其具有重量轻、强度高
基于超声检测的多层粘接结构界面脱粘缺陷的研究的开题报告.docx
基于超声检测的多层粘接结构界面脱粘缺陷的研究的开题报告1.研究背景与意义随着工业技术的不断发展,多层粘接结构在航空、航天、汽车、电子等领域得到了广泛应用。多层粘接结构通常由几层不同材料构成的复合材料组成。由于这些复合材料强度高、重量轻、防腐能力强、耐高温、耐腐蚀、吸音等特性,因此在高科技领域中应用广泛。然而,多层粘接结构在使用过程中容易发生界面脱粘现象。界面脱粘缺陷是由于材料之间粘接不牢固,或者产生微小裂纹所导致的。界面脱粘缺陷会导致材料的力学性能下降,加速材料老化,从而影响整个结构的使用寿命和安全性。因
基于超声检测的多层粘接结构界面脱粘缺陷的研究的任务书.docx
基于超声检测的多层粘接结构界面脱粘缺陷的研究的任务书任务书一、题目:基于超声检测的多层粘接结构界面脱粘缺陷的研究二、任务背景在现代工业生产中,多层粘接结构被广泛应用于汽车、飞机、火车等交通工具、计算机和通讯设备、集成电路和半导体等电子类产品。这些产品中,多层粘接结构的强度和稳定性关系到产品安全和寿命。而粘接结构的界面质量是影响其强度和稳定性的重要因素之一。因此,对界面质量的检测和评估具有重要的意义。传统的界面质量检测方法主要包括人工检验和拉伸试验等方法,这些方法虽然简单易行,但其缺点也比较明显:人工检验的
复合材料粘接结构超声声谐振检测技术.docx
复合材料粘接结构超声声谐振检测技术复合材料粘接结构超声声谐振检测技术摘要:随着复合材料在航空航天、汽车制造等领域的广泛应用,复合材料粘接结构的质量控制变得越来越重要。超声声谐振检测技术是一种无损检测方法,可以用于评估复合材料粘接结构的完整性和质量。本文对复合材料粘接结构超声声谐振检测技术进行了探讨,并介绍了其工作原理、应用领域以及发展趋势。通过实验证明,超声声谐振检测技术可以有效地检测复合材料粘接结构的缺陷,并为质量控制提供了一种可靠的方法。关键词:复合材料、粘接结构、超声声谐振检测、无损检测、质量控制1