
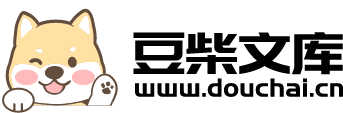
基于刀位点修改的曲面刀轨轮廓误差补偿方法.pdf
小琛****82
亲,该文档总共24页,到这已经超出免费预览范围,如果喜欢就直接下载吧~
相关资料
基于刀位点修改的曲面刀轨轮廓误差补偿方法.pdf
本发明基于刀位点修改的曲面刀轨轮廓误差补偿方法属于数控机床动态误差补偿领域,涉及一种轮廓误差估计新方法和基于刀位点修改的曲面刀轨轮廓误差补偿新方法。该方法在辨识加工进给轴控制系统伺服增益的基础上,根据随动误差模型和直线插补加工代码,离线估计实际加工点;利用理想刀轨“累加弦长参数三次样条”近似的方法估计轮廓误差矢量;再利用轮廓误差矢量在各轴的分量计算轮廓误差补偿值,得到补偿后刀位点,进而生成补偿后直线插补数控加工代码,用于实际加工。该方法是提高数控机床动态精度的刀轨轮廓误差补偿方法,精确度高,计算过程稳定,
加工进给速度优化的刀轨曲线轮廓误差补偿方法.pdf
本发明进给速度优化的刀轨曲线轮廓误差补偿方法属于复杂曲面零件高质高效加工领域,涉及一种包含进给速度优化和刀位点修改的刀轨曲线轮廓误差补偿方法。该方法根据直线插补加工代码中的刀位点和加工进给速度信息,以数控机床进给轴加速度和加加速度极限为约束,对进给速度进行优化;利用三次B样条拟合方法平滑进给速度曲线,得到最终优化后的加工进给速度;再利用刀位点和优化后进给速度,计算各轴轮廓误差补偿量,进而获得补偿后直线插补数控指令,用于实际加工,从而提高轮廓精度。该方法的实施过程仅需要修改直线插补加工代码中的刀位点和加工进
一种自由轮廓曲面铣削加工的让刀误差补偿方法.pdf
一种自由轮廓曲面铣削加工的让刀误差补偿方法,属于铣削加工制造技术领域。其特征是通过规划半精加工的刀具轨迹,优化精加工的加工余量,使得精加工过程中法向等效接触切削力保持恒定,进而保持法向让刀误差恒定。让刀误差通过法向等距偏置精加工刀具轨迹实现补偿。加工余量优化考虑了自由轮廓曲面加工过程中刀具的实际切削进给速度和切触角的变化。本发明的效果和益处是实现方法简单可靠,无需繁琐的测量和迭代计算,可以模块化实现,易于形成软件产品。
球形刀三坐标数控曲面加工误差补偿研究.docx
球形刀三坐标数控曲面加工误差补偿研究摘要:球形刀三坐标数控曲面加工误差补偿是一个非常重要的研究领域。本文研究了球形刀三坐标数控曲面加工误差的来源和影响,探讨了曲面加工误差补偿的方法,剖析了曲面加工误差补偿在提高加工精度方面的作用。关键词:球形刀、三坐标、数控曲面加工、误差补偿、加工精度一、引言在制造行业中,曲面加工精度是非常重要的一个方面,而曲面加工精度的高低取决于很多因素,例如机床精度、刀具形状、材料硬度等等。球形刀作为一种常用的数控刀具,广泛应用于汽车、航空航天、军工等行业的曲面加工中。球形刀三坐标数
镗刀杆误差补偿装置.pdf
本发明公开了一种镗刀杆误差补偿装置,包括凸轮轴、移动传动部分和转动传动部分,凸轮轴一端伸入镗刀杆中心通孔,该伸入端的轴杆上设置有凸轮,凸轮轴另一端与移动传动部分和转动传动部分连接,移动传动部分带动凸轮轴在镗刀杆中心孔中轴向移动,至凸轮移至精镗刀台所在位置,转动传动部分再带动凸轮轴旋转一定角度,驱动轴上的凸轮偏转,推动镗刀杆上的精镗刀台弹性外伸,使精镗刀至精镗尺寸的工作位置以进行精镗加工。本发明能够实现刀具磨损补偿和气缸孔圆柱度误差补偿,避免了在退刀过程中刀具在加工表面上留下退刀痕,最大限度地减少了对刀、换