
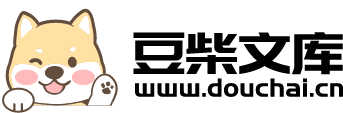
基于MFCC与CDET的滚动轴承故障诊断方法研究.docx
快乐****蜜蜂
在线预览结束,喜欢就下载吧,查找使用更方便
相关资料
基于MFCC与CDET的滚动轴承故障诊断方法研究.docx
基于MFCC与CDET的滚动轴承故障诊断方法研究基于MFCC与CDET的滚动轴承故障诊断方法研究摘要:随着工业化的快速发展,滚动轴承作为重要的传动元件,其可靠性对于保障生产安全和提高工作效率起到至关重要的作用。然而,滚动轴承的故障会导致设备停机、产生不良质量以及增加维护成本。因此,及早准确地诊断滚动轴承的故障是至关重要的。本文基于MFCC(MelFrequencyCepstralCoefficients)和CDET(ContinuousandDiscreteEnergyTransform)提出了一种滚动轴
基于MFCC的语音评分方法研究.docx
基于MFCC的语音评分方法研究基于MFCC的语音评分方法研究摘要:近年来,随着语音识别和语音合成技术的快速发展,语音评分也成为了一个重要的研究领域。在语音评分中,传统的基于声学特征的评分方法已经取得了一定的成绩,但是仍然面临着一些挑战。本文提出了一种基于MFCC的语音评分方法,通过提取语音的MFCC特征,将其作为评分的依据,实现了更准确和精确的语音评分。实验证明,本方法在语音评分中具有较高的准确率和鲁棒性。1.引言语音评分是指根据语音的质量和准确性对其进行打分的过程。语音评分在语音识别、语音合成和语音解析
基于遗传编程的滚动轴承故障诊断方法研究.docx
基于遗传编程的滚动轴承故障诊断方法研究基于遗传编程的滚动轴承故障诊断方法研究摘要:滚动轴承故障诊断是现代工业领域中的一个重要问题。针对传统的滚动轴承故障诊断方法存在的问题,本文提出了一种基于遗传编程的滚动轴承故障诊断方法。首先,详细介绍了滚动轴承故障诊断的背景和意义。然后,对滚动轴承故障的原因和特征进行了分析。接着,介绍了遗传编程的基本原理和步骤,并将其应用于滚动轴承故障诊断中。最后,通过实验验证了本文所提出方法的有效性和可行性。关键词:滚动轴承,故障诊断,遗传编程第一章引言1.1研究背景和意义滚动轴承是
基于熵理论的滚动轴承故障诊断方法研究.docx
基于熵理论的滚动轴承故障诊断方法研究摘要:滚动轴承在机械装备中起着至关重要的作用,其故障引起的机械故障事件往往会导致设备停机和维修,进一步影响工业生产的正常进行。因此,滚动轴承故障的及时检测和诊断对于设备的正常运行和故障预防至关重要。本文基于熵理论,对滚动轴承故障诊断方法进行了研究。首先,介绍了滚动轴承的工作原理和故障类型,并对滚动轴承故障诊断的重要性进行了说明。其次,详细介绍了熵理论的基本原理和应用方法,并说明了熵理论在故障诊断领域的优势。然后,根据滚动轴承故障的特点和熵理论的应用,提出了一种基于熵理论
基于递归分析的滚动轴承故障诊断方法研究.docx
基于递归分析的滚动轴承故障诊断方法研究基于递归分析的滚动轴承故障诊断方法研究摘要:随着工业技术的快速发展,滚动轴承被广泛应用于机械设备中。然而,滚动轴承故障可能会导致机械设备停机和高昂的维修成本。因此,准确、快速地识别滚动轴承故障非常重要。本论文基于递归分析方法,对滚动轴承故障诊断方法进行研究,提出了一种新的故障诊断方法,能够有效地检测和诊断滚动轴承故障。一、引言滚动轴承是一种重要的机械部件,广泛应用于各种机械设备中,如风力发电机、汽车发动机、工业机械等。然而,长期使用和负载条件可能会导致滚动轴承的磨损和