
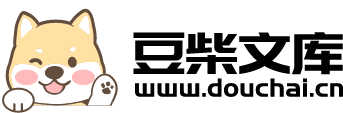
共因失效相关同级叶片系统可靠性分析.docx
快乐****蜜蜂
在线预览结束,喜欢就下载吧,查找使用更方便
相关资料
共因失效相关同级叶片系统可靠性分析.docx
共因失效相关同级叶片系统可靠性分析标题:共因失效:相关同级叶片系统的可靠性分析摘要:共因失效是指多个系统组件或元件由于同一原因或相互作用导致失效的现象。在同级叶片系统中,该现象尤为重要,因为多个叶片的失效可能会导致整个系统的失效。因此,对于相关同级叶片系统的可靠性进行分析至关重要。本文将探讨共因失效的概念、原因和影响,并介绍一种常用的可靠性分析方法。最后,我们将以一个案例研究来说明如何应用该分析方法来评估相关同级叶片系统的可靠性。关键词:共因失效,相关同级叶片系统,可靠性分析1.引言:相关同级叶片系统在许
共因失效相关同级叶片系统可靠性分析.docx
共因失效相关同级叶片系统可靠性分析共因失效相关同级叶片系统可靠性分析概述在航空工程中,叶片系统是至关重要的组成部分。叶片系统包括许多零部件,它们必须在经过数千个小时的工作后依然能够正常运转。然而,叶片系统在使用过程中会受到许多因素的影响,包括疲劳、腐蚀、高温、高压等因素。这些因素可能会导致零部件失效,从而导致叶片系统的故障。在这种情况下,共因失效分析被广泛用于叶片系统的可靠性评估。本文旨在探讨共因失效相关同级叶片系统的可靠性分析方法。1.共因失效概述共因失效指两个或多个零部件受到同一因素的影响而同时失效的
基于共因失效的海水系统多状态可靠性分析.docx
基于共因失效的海水系统多状态可靠性分析一、研究背景及意义海水系统是指在海洋工程中对海水进行加工处理的一个系统,其可靠性对于工程的顺利进行、人员的安全以及环境保护都有非常重要的意义。然而,海水系统在使用的过程中,其多种子系统、模块的失效可能会相互影响,而且失效的原因也可能有很多种,因此,如何准确地分析海水系统的可靠性,对于海洋工程的实际操作非常关键。二、海水系统的多状态可靠性分析方法1.共因失效的概念及影响共因失效,指的是若干个设备在共同作用环境下,由于共同的外部因素或共同的内部状态引起的设备失效,是造成海
基于共因失效的海水系统多状态可靠性分析.docx
基于共因失效的海水系统多状态可靠性分析海水系统是一种十分重要的系统,它的功能是根据需要将海水净化和处理为能够在海上使用的水源。由于其特殊的运行环境,海水处理系统的可靠性在保证船只的正常运转和船员安全之间扮演着至关重要的角色。本文将基于共因失效理论,探讨海水系统多状态可靠性分析。1.共因失效理论共因失效是指两个或多个系统组成的某个组件或部件因相同的原因而失效。这种失效是不可避免的,并且会对整个系统的可靠性产生重大影响。共因失效的原因可能是设计缺陷、材料劣化、操作错误等。为了提高系统可靠性并减少共因失效的影响
基于贝叶斯网络的多状态共因失效系统可靠性分析.docx
基于贝叶斯网络的多状态共因失效系统可靠性分析基于贝叶斯网络的多状态共因失效系统可靠性分析摘要:随着现代工程系统的复杂性不断增加,对系统可靠性的研究也越来越受到重视。贝叶斯网络作为一种概率图模型,可以有效地进行多状态共因失效系统的可靠性分析。本文主要介绍了贝叶斯网络的基本原理和应用于多状态共因失效系统可靠性分析的方法,并通过一个实际案例深入探讨了该方法的有效性和可行性。关键词:贝叶斯网络;多状态共因失效系统;可靠性分析引言:多状态共因失效系统是指系统的部件之间存在相互依赖关系,并且系统的失效模式可能有多种状