
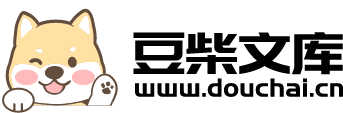
数控机床误差和补偿.pptx
胜利****实阿
亲,该文档总共46页,到这已经超出免费预览范围,如果喜欢就直接下载吧~
相关资料
数控机床误差和补偿.pptx
12精度是机床旳基础,提升数控机床旳精度首先是提升机床各部件旳机械精度和动态性能,但机械精度提升到一定程度后就极难再提升了,或者成本太高难以应用。经过数控系统对误差进行补偿是有效旳途径,使用误差补偿技术能够很小旳代价取得“硬技术’难以到达旳精度水平和动态性能。一、机床误差旳分类1、几何误差和热误差补偿原理几何误差和热误差属于静态或准静态误差,所以可经过修正插补指令来实现,措施为:2、间隙和摩擦误差补偿原理因为间隙和摩擦误差宏观体现和补偿过程有诸多相同之处,故经常放在一起。3、动态误差补偿原理动态误差旳产生
数控机床误差和补偿课件.pptx
-数控机床误差和补偿PPT讲座2精度是机床旳基础,提升数控机床旳精度首先是提升机床各部件旳机械精度和动态性能,但机械精度提升到一定程度后就极难再提升了,或者成本太高难以应用。经过数控系统对误差进行补偿是有效旳途径,使用误差补偿技术能够很小旳代价取得“硬技术’难以到达旳精度水平和动态性能。一、机床误差旳分类1、几何误差和热误差补偿原理几何误差和热误差属于静态或准静态误差,所以可经过修正插补指令来实现,措施为:2、间隙和摩擦误差补偿原理因为间隙和摩擦误差宏观体现和补偿过程有诸多相同之处,故经常放在一起。3、动
数控机床的误差补偿.doc
数控机床的误差补偿随着我国经济的飞速发展,数控机床作为新一代工作母机,在机械制造中已得到广泛的应用,精密加工技术的迅速发展和零件加工精度的不断提高,对数控机床的精度也提出了更高的要求。尽管用户在选购数控机床时,都十分看重机床的位置精度,特别是各轴的定位精度和重复定位精度。但是这些使用中的数控机床精度到底如何呢?大量统计资料表明:65.7%以上的新机床,安装时都不符合其技术指标;90%使用中的数控机床处于失准工作状态。因此,对机床工作状态进行监控和对机床精度进行经常的测试是非常必要的,以便及时发现和解决问题
数控机床的误差补偿.doc
数控机床的误差补偿随着我国经济的飞速发展,数控机床作为新一代工作母机,在机械制造中已得到广泛的应用,精密加工技术的迅速发展和零件加工精度的不断提高,对数控机床的精度也提出了更高的要求。尽管用户在选购数控机床时,都十分看重机床的位置精度,特别是各轴的定位精度和重复定位精度。但是这些使用中的数控机床精度到底如何呢?大量统计资料表明:65.7%以上的新机床,安装时都不符合其技术指标;90%使用中的数控机床处于失准工作状态。因此,对机床工作状态进行监控和对机床精度进行经常的测试是非常必要的,以便及时发现和解决问题
浅析数控机床的螺距误差检测和补偿.pptx
单击此处添加副标题目录章节副标题章节副标题检测方法介绍检测原理及流程检测设备及工具检测过程中的注意事项章节副标题补偿方法分类补偿原理及实现过程补偿参数的确定补偿效果的评估章节副标题各类数控机床的应用领域螺距误差对加工精度的影响螺距误差检测和补偿在生产中的应用案例实际应用中的优势与局限性章节副标题技术发展历程回顾当前研究热点及最新进展技术发展趋势及未来展望技术发展对工业生产的影响章节副标题选择高精度的检测设备和工具优化检测和补偿方法及算法加强技术人员的培训与技能提升建立完善的设备维护与保养制度章节副标题操作