
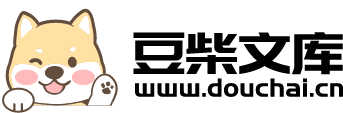
基于ANSYS的轮轨滚动接触疲劳裂纹萌生研究.docx
快乐****蜜蜂
在线预览结束,喜欢就下载吧,查找使用更方便
相关资料
基于ANSYS的轮轨滚动接触疲劳裂纹萌生研究.docx
基于ANSYS的轮轨滚动接触疲劳裂纹萌生研究摘要本文以ANSYS为工具,研究了轮轨滚动接触下的疲劳裂纹萌生特性。通过构建轮轨滚动接触模型,利用有限元分析方法,考虑了材料的非线性本质以及疲劳载荷的作用,探究了轮轨接触表面上的疲劳裂纹萌生规律。研究结果表明,界面处应力集中导致了轮轨接触表面的疲劳裂纹萌生,而裂纹数量和深度与载荷及材料本身的性质密切相关。本研究可为轮轨接触表面结构设计及轨道维护提供参考依据。关键词:疲劳裂纹萌生;轮轨接触;ANSYS;有限元分析;应力集中引言轮轨接触是列车行驶中至关重要的环节,其
高速铁路轮轨滚动接触疲劳裂纹萌生及扩展的有限元分析.docx
高速铁路轮轨滚动接触疲劳裂纹萌生及扩展的有限元分析高速铁路是一种高速公共交通工具,其性能和安全性是使用者最为关心的问题。其中,轮轨滚动接触疲劳裂纹的萌生和扩展是高速铁路运行中的一个非常重要的问题。本文将介绍高速铁路轮轨滚动接触疲劳裂纹萌生及扩展的有限元分析。第一部分:问题概述高速铁路的轮轨滚动接触疲劳裂纹是一种疲劳破坏的形式。这种疲劳裂纹的萌生通常是由于动荷载引起的,如铁路车辆的运行和优化的轮轨接触表面造成的。当裂纹发展到一定深度时,会严重影响高速铁路的安全性和性能。由于铁路制造工艺、运营条件、材料性能等
轮轨滚动接触疲劳裂纹的动态扩展研究的开题报告.docx
轮轨滚动接触疲劳裂纹的动态扩展研究的开题报告一、选题背景及研究意义轮轨作为铁路交通中最基本的组成部分,其运行状态的稳定性和安全性直接关系到铁路线路的运营效益以及广大人民群众的出行安全。在铁路交通中,轮轨接触是最基础也是最重要的一环。而轮轨接触的疲劳裂纹是造成铁路车辆运行安全事故的主要原因之一。因此,研究轮轨接触疲劳裂纹的动态扩展规律,对于铁路交通的安全稳定运行有着重要的意义。目前,国内外对于轮轨接触疲劳裂纹的研究主要集中在静态力学试验和数值模拟两个方面。然而,轮轨接触过程中裂纹的动态扩展规律研究却较为缺乏
轮轨高速滚动接触及钢轨疲劳裂纹扩展研究.docx
轮轨高速滚动接触及钢轨疲劳裂纹扩展研究轮轨高速滚动接触及钢轨疲劳裂纹扩展研究摘要轮轨高速滚动接触及钢轨疲劳裂纹扩展是铁路运输行业的一个重大问题。本文对轮轨高速滚动接触及钢轨疲劳裂纹扩展进行了深入研究。首先介绍了轮轨高速滚动接触及钢轨疲劳裂纹扩展的背景及意义。然后,分析了轮轨高速滚动接触的原因及其对铁路运输的影响。接着,对钢轨疲劳裂纹的形成及传播机制进行了探讨。最后,本文提出了预防和控制轮轨高速滚动接触及钢轨疲劳裂纹扩展的策略。关键词:轮轨高速滚动接触;钢轨疲劳裂纹;铁路运输;预防策略;控制策略Abstra
高速铁路轮轨滚动接触疲劳裂纹萌生及扩展的有限元分析的任务书.docx
高速铁路轮轨滚动接触疲劳裂纹萌生及扩展的有限元分析的任务书任务书研究背景:作为交通运输领域的重要组成部分,高速铁路的运营速度和运行里程在不断提高,这也要求铁路轮轨系统具备更高的耐久性和安全性。然而,随着轮轨间接触力的不断增大,轮轨滚动接触会产生一系列的疲劳问题,如疲劳裂纹的萌生和扩展等,这些问题对于铁路轮轨系统的安全稳定运行至关重要。研究内容:本项目旨在对高速铁路轮轨滚动接触疲劳裂纹萌生及扩展进行有限元分析,具体内容包括以下两个方面:1.研究滚动接触疲劳裂纹萌生机理。通过模拟高速铁路轮轨系统的滚动接触过程