
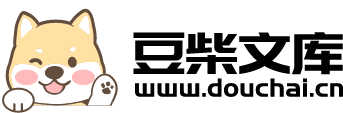
基于机器学习的灭弧栅片表面缺陷检测方法.docx
快乐****蜜蜂
在线预览结束,喜欢就下载吧,查找使用更方便
相关资料
基于机器学习的灭弧栅片表面缺陷检测方法.docx
基于机器学习的灭弧栅片表面缺陷检测方法标题:基于机器学习的灭弧栅片表面缺陷检测方法摘要:随着现代科技的发展,灭弧栅片被广泛应用于高压开关设备中,起到确保设备工作稳定可靠的作用。然而,灭弧栅片在使用过程中可能会出现表面缺陷,如裂纹、磨损和氧化等,这些缺陷可能导致设备性能下降甚至故障。因此,对灭弧栅片表面缺陷进行准确可靠的检测具有重要意义。本论文针对灭弧栅片的表面缺陷检测问题,提出了一种基于机器学习的方法。通过采集灭弧栅片的表面图像数据,建立了一个灭弧栅片表面缺陷检测模型,并利用该模型进行缺陷的自动识别。实验
灭弧栅片、灭弧室以及断路器.pdf
本发明涉及一种灭弧栅片及其灭弧室,其为一片状体,其特征在于:所述灭弧栅片的片状体是由一片材对折而成,使之具有上下相叠的上层部分和下层部分,上层部分和下层部分之间留有间隙,且所述上层部分和下层部分的间隙中嵌置有一片状绝缘件。本发明是在灭弧栅片中增加一片状绝缘件,有效降低相邻短弧串成一体的概率,为断路器的小型化、分断能力的进一步提升提供支持。
基于机器学习的木材表面缺陷图像检测及应用.docx
基于机器学习的木材表面缺陷图像检测及应用基于机器学习的木材表面缺陷图像检测及应用摘要:随着木材的广泛应用,对木材表面缺陷的检测变得越来越重要。传统的人工检测方式费时费力且准确率有限。为了解决这个问题,本文提出了一种基于机器学习的木材表面缺陷图像检测方法。该方法利用了计算机视觉和机器学习技术,通过训练一种缺陷检测模型,实现对木材表面缺陷的自动化检测。实验结果表明,该方法具有较高的准确率和较快的检测速度,可有效提高木材质量的检测效率,为木材行业提供了一种新的检测手段。关键词:机器学习,木材表面缺陷,图像检测,
基于机器视觉的混凝土构件表面缺陷检测方法.pptx
汇报人:目录PARTONEPARTTWO机器视觉技术的定义和原理机器视觉技术在混凝土构件检测中的应用机器视觉技术的优势和局限性PARTTHREE混凝土构件表面缺陷类型表面缺陷检测的难点和挑战传统检测方法的局限性和不足PARTFOUR图像采集和处理特征提取和选择缺陷分类和识别检测结果的评估和优化PARTFIVE实验环境和数据集实验方法和过程实验结果及分析结果与现有方法的比较PARTSIX基于机器视觉的混凝土构件表面缺陷检测方法的应用前景未来研究方向和挑战技术推广和实际应用价值THANKYOU
基于机器视觉的混凝土构件表面缺陷检测方法.docx
基于机器视觉的混凝土构件表面缺陷检测方法基于机器视觉的混凝土构件表面缺陷检测方法摘要:混凝土结构的表面缺陷对其性能和寿命有着重要的影响。当前常见的表面缺陷检测方法主要依赖于人工目视和手工测量,因而具有效率低下、误判率高等缺陷。机器视觉作为一种非接触式的检测手段,在混凝土结构表面缺陷检测领域有着广泛的应用前景。本文介绍了机器视觉在混凝土结构表面缺陷检测方面的基本原理和主要方法。通过实验验证,提出的基于机器视觉的混凝土结构表面缺陷检测方法具有较高的检测精度和效率,可以满足实际工程应用的需求。关键词:机器视觉;