
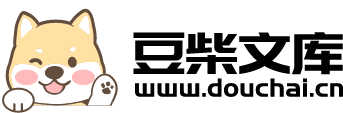
基于组合降噪的卷积神经网络轴承故障诊断方法.docx
快乐****蜜蜂
在线预览结束,喜欢就下载吧,查找使用更方便
相关资料
基于组合降噪的卷积神经网络轴承故障诊断方法.docx
基于组合降噪的卷积神经网络轴承故障诊断方法基于组合降噪的卷积神经网络轴承故障诊断方法摘要:随着工业机械的不断发展,轴承故障诊断成为保证设备安全运行的重要手段之一。然而,轴承信号中常常受到噪声和干扰的影响,导致传统的故障诊断方法效果不佳。为了解决这一问题,本文提出了一种基于组合降噪的卷积神经网络轴承故障诊断方法。该方法首先使用小波变换进行信号去噪,然后采用卷积神经网络进行特征提取和分类诊断。实验结果表明,该方法能够有效地提高轴承故障诊断的准确率和稳定性。1.引言轴承作为工业机械中的重要部件,在设备的正常运行
基于卷积神经网络的轴承故障诊断方法.pptx
基于卷积神经网络的轴承故障诊断方法目录添加目录项标题卷积神经网络的基本原理卷积神经网络的结构卷积神经网络的学习过程卷积神经网络在图像识别中的应用轴承故障诊断的重要性轴承故障对机械设备的影响传统轴承故障诊断方法的局限性基于卷积神经网络的轴承故障诊断方法的优势基于卷积神经网络的轴承故障诊断方法数据预处理特征提取分类器设计训练和测试过程实验结果与分析实验数据集介绍实验结果展示结果分析与传统方法的比较实际应用与展望基于卷积神经网络的轴承故障诊断方法在实际生产中的应用该领域未来的研究方向感谢观看
基于一维卷积神经网络的轴承故障诊断方法研究.docx
基于一维卷积神经网络的轴承故障诊断方法研究基于一维卷积神经网络的轴承故障诊断方法研究摘要:近年来,随着机械设备的广泛应用,轴承故障的预防与诊断愈发重要。为了提高轴承故障的诊断准确性和效率,本文研究了基于一维卷积神经网络的轴承故障诊断方法。首先,我们介绍了卷积神经网络的基本原理和轴承故障的常见类型。然后,我们提出了一种基于一维卷积神经网络的轴承故障诊断模型,并详细阐述了该模型的设计思路和流程。最后,我们通过实验验证了该方法的有效性和优越性。关键词:一维卷积神经网络;轴承故障;诊断方法;故障类型;实验验证1.
基于短时傅里叶变换和卷积神经网络的轴承故障诊断方法.docx
基于短时傅里叶变换和卷积神经网络的轴承故障诊断方法摘要轴承故障是机械设备常见的故障之一。如何有效地诊断轴承故障,是提高机械设备可靠性和运行效率的关键。本文提出了一种基于短时傅里叶变换和卷积神经网络的轴承故障诊断方法。通过对轴承信号进行短时傅里叶变换,得到轴承信号在时序和频域上的特征。然后将这些特征输入到卷积神经网络中进行训练和诊断。实验结果表明,本文所提出的方法能够有效地诊断轴承故障,并且具有较高的准确率和鲁棒性。关键词:轴承故障;短时傅里叶变换;卷积神经网络;特征提取;诊断1.引言轴承是机械设备中常见的
基于卷积神经网络滚动轴承故障诊断建模方法研究.docx
基于卷积神经网络滚动轴承故障诊断建模方法研究基于卷积神经网络滚动轴承故障诊断建模方法研究摘要:滚动轴承是旋转设备中最常见也是最容易发生故障的部件之一,其故障诊断对于设备的安全运行和预测维护至关重要。本文针对滚动轴承故障诊断问题,提出了一种基于卷积神经网络的建模方法。首先,我们收集了滚动轴承的振动信号数据,并对其进行特征提取和预处理。然后,我们设计了一个卷积神经网络模型,并使用该模型来训练和测试滚动轴承的故障诊断模型。实验结果表明,该方法在滚动轴承故障预测和诊断方面具有较高的准确性和可靠性。关键词:滚动轴承