
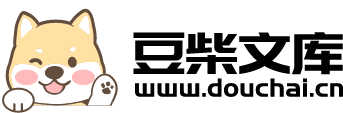
SiCpAl复合材料的制备及其性能研究.docx
快乐****蜜蜂
在线预览结束,喜欢就下载吧,查找使用更方便
相关资料
SiCpAl复合材料的制备及其性能研究.docx
SiCpAl复合材料的制备及其性能研究SiCpAl复合材料的制备及其性能研究摘要:SiCpAl复合材料由于其优异的物理、化学以及力学性能,在航空航天、汽车、电子器件等领域得到了广泛应用。本文综述了SiCpAl复合材料的制备方法,包括粉末冶金法、固相反应法和浸渍法等。同时,还对其性能进行了研究,包括力学性能、热性能和电性能等。研究结果表明,SiCpAl复合材料具有较高的强度、硬度和热稳定性,适用于高温和高强度的应用。1.引言SiCpAl复合材料是将SiC陶瓷颗粒加入到Al基体中制备而成的复合材料。SiC陶瓷
SiCpAl复合材料的制备工艺及性能研究的任务书.docx
SiCpAl复合材料的制备工艺及性能研究的任务书任务书课题名称:SiCpAl复合材料的制备工艺及性能研究一、研究背景和目的随着现代工业的发展,对于高性能、轻质、高强度材料的需求越来越高。SiCpAl复合材料具有较好的抗热冲击性能、高强度、优异的耐腐蚀性能等特点,因此在航空、汽车、能源等领域具有广阔的应用前景。本课题旨在研究SiCpAl复合材料的制备工艺以及相关性能,为其应用提供技术支持。二、研究内容和方法1.制备工艺的研究:(1)调整SiC颗粒的尺寸和含量,优化颗粒的分散性。(2)研究不同形式的Al基体中
体育器材用SiCpAl复合材料的制备和性能研究.docx
体育器材用SiCpAl复合材料的制备和性能研究引言在体育器材的制造过程中,选择材料是一个非常重要的环节。随着科技的不断发展,复合材料在各个领域中得到了广泛应用,其具有较高的物理力学性能、良好的耐化学性和耐热性能等优点。本文选取SiCpAl复合材料作为研究对象,探讨其制备及性能。制备方法1.准备原料本实验所需的原料有纯度99%的铝粉和SiCp(SiC颗粒)。铝粉经过筛选得到,颗粒度为30-50µm;SiCp粒子大小在1-10µm之间。两种材料的用量按照质量比1:1计算。2.制备过程将铝粉和SiCp在球磨机中
SiCpAl复合材料的力学性能研究.docx
SiCpAl复合材料的力学性能研究摘要:SiCpAl复合材料是以陶瓷颗粒(SiCp)作为增韧相,在铝基合金基体材料中形成了细小且分布均匀的加强相,使得复合材料具有高强度、高硬度和较好的耐磨性等优良的力学性能。本文概述了SiCpAl复合材料的力学性能研究进展。介绍了制备SiCpAl复合材料的方法和工艺,重点论述了SiCpAl结构、力学性能和微观细观结构之间的关系。分析了制备工艺对SiCpAl复合材料性能的影响,并指出了未来应该加强对SiCpAl复合材料微观结构及力学性能之间相互作用机制的深入研究。关键词:S
SiCpAl基复合材料表面Ni--P镀层的制备工艺与性能研究.docx
SiCpAl基复合材料表面Ni--P镀层的制备工艺与性能研究摘要:本文研究了SiCpAl基复合材料表面Ni--P镀层的制备工艺与性能。首先通过化学法制备了具有一定晶粒度的SiC粉末,并与Al基体进行混合,制备得到SiCpAl基复合材料。接着采用电化学沉积的方法,在复合材料表面沉积Ni--P合金镀层。通过扫描电镜(SEM)、能谱分析(EDS)和X射线衍射(XRD)等测试手段对制备得到的镀层的微观形貌、元素组成和晶体结构进行了表征。此外,还通过硬度测试和摩擦磨损测试分析了镀层的性能。研究结果显示,制备得到的S