
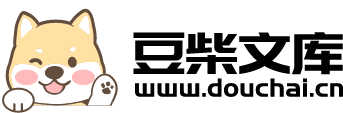
10Ni3MnCuAl高速铣削表面粗糙度实验研究及参数优化.docx
快乐****蜜蜂
在线预览结束,喜欢就下载吧,查找使用更方便
相关资料
10Ni3MnCuAl高速铣削表面粗糙度实验研究及参数优化.docx
10Ni3MnCuAl高速铣削表面粗糙度实验研究及参数优化摘要:高速铣削作为一种重要的精密加工技术,在工业生产中得到广泛应用。本文基于10Ni3MnCuAl材料进行高速铣削实验,探究其表面粗糙度的变化规律,并通过参数优化的方法提高表面质量。实验结果表明,高速铣削的加工表面粗糙度较低,通过优化加工参数,可进一步提高表面质量。关键词:高速铣削;表面粗糙度;参数优化;10Ni3MnCuAl材料1.引言高速铣削作为一种高效、高精度的加工技术,近年来得到了广泛的应用。它具有能够提高生产效率、减少生产成本以及提高加工
高速铣削AlMn1Cu表面粗糙度变化规律及铣削参数优化研究.docx
高速铣削AlMn1Cu表面粗糙度变化规律及铣削参数优化研究摘要:本文研究了高速铣削AlMn1Cu表面粗糙度的变化规律及铣削参数的优化。通过实验测量得到了不同铣削参数下的表面粗糙度数据,并利用正交试验法分析优化结果。结果表明:切削深度和进给速度是主要影响因素,且二者互相作用影响显著;通过合理地选择切削深度和进给速度等铣削参数,可以有效地控制AlMn1Cu的表面粗糙度。关键词:高速铣削;表面粗糙度;AlMn1Cu;铣削参数优化。一、引言高速铣削是一种重要的加工方法,广泛应用于汽车、航空航天等领域。在高速铣削过
SLM成型件铣削表面粗糙度预测模型及参数优化研究.docx
SLM成型件铣削表面粗糙度预测模型及参数优化研究SLM成型件铣削表面粗糙度预测模型及参数优化研究摘要:近年来,选择性激光熔化(SLM)技术作为一种高精度的快速成型技术,被广泛应用于航空、医疗、汽车等领域。然而,由于SLM成型后的零件表面粗糙度较高,需要进行后续的加工工艺来提高表面质量。因此,本文主要研究了SLM成型件铣削表面粗糙度预测模型及参数优化。引言:SLM成型技术是一种通过激光将金属粉末熔化成立体零件的快速成型技术。在SLM成型后的零件表面粗糙度较高,会影响到其使用性能和外观质量。因此,需要采用后续
基于田口试验法的铣削加工表面粗糙度与铣削参数优化.docx
基于田口试验法的铣削加工表面粗糙度与铣削参数优化基于田口试验法的铣削加工表面粗糙度与铣削参数优化摘要:表面粗糙度是衡量铣削加工质量的重要指标之一。本文基于田口试验法,通过对铣削加工过程中的铣削参数进行优化研究,来提高铣削加工表面粗糙度的质量。关键词:铣削加工;表面粗糙度;田口试验法;铣削参数优化一、引言铣削是一种常见的金属加工方法,其应用广泛,并且对加工质量有重要影响的是加工表面粗糙度。因此,如何根据铣削加工的需求,优化铣削过程中的参数,提高加工表面的粗糙度成为本文研究的重点。田口试验法是一种设计实验参数
高速铣削铸铝半圆弧工件表面粗糙度的实验研究.docx
高速铣削铸铝半圆弧工件表面粗糙度的实验研究本论文探讨了高速铣削铸铝半圆弧工件表面粗糙度的实验研究。通过实验比较,讨论了不同铣削参数对表面粗糙度和加工效率的影响,以及针对不同应用场合的前景和推广性。一、引言铝及其合金是重要的结构材料,被广泛应用于各种领域,如汽车、航空航天、电子、通信、纺织、印刷等。高速铣削是一种主要的加工方式之一,具有高效率、高质量、高精度等优点。将工件表面粗糙度控制在一定范围内是提高加工质量和工件性能的关键之一。因此,研究铸铝半圆弧工件表面粗糙度的加工技术具有重要的意义。二、实验装置和方