
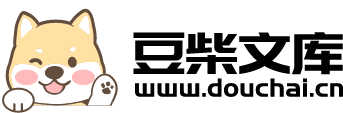
无芯模旋压回弹变形特性及多道次轨迹规划方法仿真研究.docx
快乐****蜜蜂
在线预览结束,喜欢就下载吧,查找使用更方便
相关资料
无芯模旋压回弹变形特性及多道次轨迹规划方法仿真研究.docx
无芯模旋压回弹变形特性及多道次轨迹规划方法仿真研究无芯模旋压回弹变形特性及多道次轨迹规划方法仿真研究摘要:本文利用数值模拟方法研究了无芯模旋压回弹变形特性及多道次轨迹规划方法,首先对模旋压基本过程进行简要介绍和分析,以及回弹过程的物理意义和影响因素。接着,通过建立有限元模型进行模拟计算,得到了模旋压过程中的应力、应变、变形等关键参数,并对多种回弹措施进行模拟,并对结果进行对比和分析。最后,提出了一种基于优化算法的多次道次轨迹规划方法,经过仿真验证,能够有效地提高生产效率和产品质量。关键词:无芯模旋压;回弹
无芯模旋压回弹变形特性及多道次轨迹规划方法仿真研究的开题报告.docx
无芯模旋压回弹变形特性及多道次轨迹规划方法仿真研究的开题报告一、研究背景随着社会的不断发展和变化,机械加工行业也面临着越来越大的挑战和机遇。在机械加工过程中,模具工艺技术一直都是关键的环节。其中,无芯模旋压回弹变形特性及多道次轨迹规划方法,是目前热门的研究领域之一。由于无芯模旋压回弹变形特性及多道次轨迹规划方法在模具制造中的应用价值具有很高的实用性和研究意义,因此有必要对其进行深入研究。二、研究内容本文将主要从以下几个方面进行研究:1.分析无芯模旋压回弹变形特性的机理以及影响因素,通过数值模拟方法对其进行
无芯模旋压回弹变形特性及多道次轨迹规划方法仿真研究的任务书.docx
无芯模旋压回弹变形特性及多道次轨迹规划方法仿真研究的任务书一、课题背景无芯模旋压回弹变形特性及多道次轨迹规划方法是现代制造业中的重要研究方向之一,具有重要的理论意义和广泛的应用前景。随着工业生产技术的不断发展,无芯模旋压成型技术已经被广泛应用于汽车、航空航天、电子、轻工等领域。其中,无芯模旋压成型技术是一种基于模板装配、压制和加热的工艺,可以将类似于无芯板的厚壁形状加工成符合要求的准二维薄板形状。而回弹变形则是无芯模旋压成型过程中需要重点考虑的问题之一。当前,无芯模旋压回弹变形特性及多道次轨迹规划方法的研
多道次无芯模旋压成形方式及其优化研究的开题报告.docx
多道次无芯模旋压成形方式及其优化研究的开题报告一、研究背景无芯模旋压成形技术是一种高效、低成本、高精度的工艺方法,其主要应用于制造各类轴对称类零件。该工艺方法主要通过将金属板材经过一定的形状设计后,在不加热的情况下将其压制成对应形状的零件。由于该工艺方法可避免焊接、冲裁等传统工艺方法所带来的一系列制造缺陷,并且具有较好的成形精度、工件表面质量和强度等特点,因此在航空航天、汽车、机械制造等领域得到了广泛应用。目前,虽然无芯模旋压成形技术已经得到了广泛应用,但仍然存在一些问题,比如成形精度不够高、清洗成本较高
基于加工量的无芯模旋压旋轮轨迹规划与进给比优化研究.docx
基于加工量的无芯模旋压旋轮轨迹规划与进给比优化研究基于加工量的无芯模旋压旋轮轨迹规划与进给比优化研究摘要:无芯模旋压技术是一种高效率、高精度的金属加工方法。在无芯模旋压过程中,旋轮轨迹规划和进给比的选择对加工质量和生产效率有着重要影响。本文以加工量为目标,通过优化旋压轨迹和调整进给比,实现了无芯模旋压工艺的优化。通过数值模拟和实验验证,结果表明该方法能够提高加工质量和生产效率。关键词:无芯模旋压,旋轮轨迹规划,进给比,优化研究1.引言无芯模旋压是一种通过旋转压制金属工件来改变其几何形状的加工方法。与传统模