
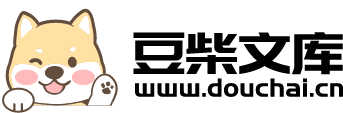
钛板的热拉深成形性与工艺参数.docx
快乐****蜜蜂
在线预览结束,喜欢就下载吧,查找使用更方便
相关资料
钛板的热拉深成形性与工艺参数.docx
钛板的热拉深成形性与工艺参数钛板的热拉深成形性与工艺参数摘要:钛合金广泛应用于航空航天、汽车、装备制造等领域,而钛板的制造工艺中,热拉深成形是一种常用且关键的方法。本论文旨在探讨钛板的热拉深成形性及相关工艺参数的研究现状和影响因素,并对其进行分析与总结。引言:钛合金作为一种重要的结构材料具有优秀的机械性能和高温耐性,因此在航空航天、船舶、汽车、医疗器械等领域得到了广泛应用。钛板的加工制造过程中,热拉深成形是一种常用的工艺方法,它能够使钛板获得复杂的形状和几何结构。然而,热拉深成形性与工艺参数之间的关系尚未
钼板热拉深成形研究.docx
钼板热拉深成形研究钼板热拉深成形研究摘要:钼板是一种重要的金属材料,具有优良的高温耐性、良好的机械性能和化学稳定性。钼板在航空航天、核能技术、电子与光电子领域具有广泛应用。钼板的成形工艺对于其性能和应用范围具有重要影响。本论文以钼板热拉深成形为研究对象,探究热处理条件对钼板热拉深成形的影响,为钼板的成形加工提供理论依据。关键词:钼板;热拉深成形;热处理;机械性能1.引言钼是一种重要的金属材料,其具有高熔点、高密度和良好的高温耐性等优点,因此在航空、航天、核能技术、电子与光电子领域得到广泛应用。钼板作为钼材
汽车后地板加强板拉深成形过程工艺参数优化的研究.docx
汽车后地板加强板拉深成形过程工艺参数优化的研究引言汽车后地板是汽车底盘系统中重要的零部件之一,它能够有效地增强车身的稳定性和承载能力。然而在汽车制造过程中,后地板往往需要经过拉深成形加工,以适应汽车车身的形状和尺寸。本文旨在通过研究汽车后地板加强板拉深成形过程的工艺参数优化,从而提高汽车零部件加工质量和生产效率。研究方法本文主要采用实验方法和数值模拟方法来研究汽车后地板加强板拉深成形过程的工艺参数优化。首先,本文将采用有限元模拟软件对后地板加强板拉深成形过程进行数值模拟分析,得出模拟结果并进行后续处理和优
工艺参数对AZ31镁合金板拉深成形性能的影响.docx
工艺参数对AZ31镁合金板拉深成形性能的影响摘要:AZ31镁合金因其轻量、高强度、高刚性等优良物理性能而备受关注。其中,在加工方面,拉深成形是一种常见的加工方式。本文研究了不同工艺参数对AZ31镁合金板拉深成形性能的影响,研究结果表明,选择合适的工艺参数可以有效提高AZ31镁合金板的拉深成形性能。关键词:AZ31镁合金板,拉深成形,工艺参数绪论:AZ31镁合金是一种轻质的高强度材料,因此在航空、汽车、电子、医疗等领域具有广泛的应用前景。在加工方面,拉深成形是一种常见的成形工艺,可以用于生产汽车、航空航天器
汽车后地板加强板拉深成形过程工艺参数优化的研究的中期报告.docx
汽车后地板加强板拉深成形过程工艺参数优化的研究的中期报告本研究旨在优化汽车后地板加强板拉深成形过程中的工艺参数。本中期报告主要介绍了研究的背景、研究现状、研究方法、实验结果和讨论。一、研究背景和现状汽车后地板加强板是汽车底盘的一个重要部件,起到了加强车身结构、提高车身刚度、减小噪音和振动等作用。而加强板的成形质量直接影响汽车的质量和安全性能。因此,如何优化加强板的成形工艺参数是一个热门的研究领域。目前,国内外学者已经通过实验和数值模拟研究了多种加强板的成形工艺,如圆锥法、逆三角法、局部提升法等。然而,对于