
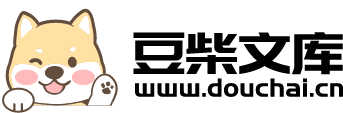
热连粗轧机支持辊剥落影响因素的有限元分析.docx
快乐****蜜蜂
在线预览结束,喜欢就下载吧,查找使用更方便
相关资料
热连粗轧机支持辊剥落影响因素的有限元分析.docx
热连粗轧机支持辊剥落影响因素的有限元分析标题:热连粗轧机支持辊剥落影响因素的有限元分析摘要:热连粗轧机是冶金工业中的一种重要设备,用于将热金属坯料压制成所需的形状和尺寸。然而,由于长期工作的高温、高压和高负荷环境,热连粗轧机的辊剥落问题成为了影响设备安全运行和生产效率的主要因素之一。本研究利用有限元分析方法,针对热连粗轧机支持辊剥落问题进行了深入探讨。通过建立辊和轧辊摩擦耦合模型,分析了辊剥落现象的产生机理,并通过有限元模拟分析了几个主要影响因素的作用机制。第一部分:引言1.研究背景和意义2.研究目的第二
不锈钢热连轧机粗轧支持辊剥落影响因素的有限元分析.docx
不锈钢热连轧机粗轧支持辊剥落影响因素的有限元分析一、前言不锈钢热连轧机是一种重要的冶炼设备,其主要用于精炼不锈钢材料。不锈钢热连轧机的粗轧支持辊是其重要组成部分之一,其性能的优劣影响着热连轧机的生产效率和品质。然而,在不锈钢热连轧机的生产实践中,粗轧支持辊的剥落现象会时有发生,严重影响了设备的生产效率和经济效益。因此,对不锈钢热连轧机粗轧支持辊剥落影响因素进行研究和分析,具有重要的意义。二、研究方法和流程本论文采用有限元分析法,通过建立不锈钢热连轧机粗轧支持辊的有限元模型,模拟粗轧支持辊受载过程,分析和评
不锈钢热连轧粗轧机支持辊剥落问题研究.docx
不锈钢热连轧粗轧机支持辊剥落问题研究一、引言不锈钢是一种优质的合金钢,由于其良好的耐腐蚀性和机械性能,在船舶、化工设备、医疗器械等领域得到广泛应用。不锈钢在生产加工过程中需要通过热轧工艺进行精细加工,保证其优良的性能和质量。在热连轧粗轧机工艺中,支持辊是不可或缺的部分,它起到支撑和传递轧制力的作用。但是,支持辊的剥落问题一直是制约不锈钢热轧工艺安全稳定生产的一个难点。针对以上问题,本文对不锈钢热连轧粗轧机支持辊剥落问题进行了研究。首先,分析了支持辊剥落的原因,然后对机械设备和工艺参数方面的优化进行了探讨,
不锈钢热连轧粗轧机支持辊剥落问题研究的开题报告.docx
不锈钢热连轧粗轧机支持辊剥落问题研究的开题报告一、选题依据不锈钢产业是我国重要的金属制造业之一,其中热连轧粗轧机是生产不锈钢的重要设备之一。在不锈钢生产过程中,由于工作条件的恶劣和高温高压等因素,粗轧机支持辊易出现剥落现象。这不仅影响了设备的正常生产,还会造成严重的安全隐患。因此,研究不锈钢热连轧粗轧机支持辊剥落问题,对提高生产安全和生产效率具有重要意义。二、选题研究意义1.能够提高设备的安全性能,降低设备的维修成本。2.可以有效地解决热连轧粗轧机支持辊剥落问题,提高生产效率。3.能够提高不锈钢生产的质量
不锈钢热连轧粗轧机支持辊剥落问题研究的任务书.docx
不锈钢热连轧粗轧机支持辊剥落问题研究的任务书任务书题目:不锈钢热连轧粗轧机支持辊剥落问题研究任务背景:热连轧粗轧机是不锈钢连轧生产线中重要的设备之一,属于钢板成型设备的范畴,主要用于对不锈钢热轧坯料进行粗轧加工,形成需要的厚度、宽度、长度的不锈钢板材,是不锈钢连轧生产过程中的一道关键工序。然而,在热连轧粗轧机的运行过程中,常常会出现支持辊剥落的问题,严重影响生产效率和产品质量。任务描述:本次任务旨在通过对不锈钢热连轧粗轧机支持辊剥落问题的研究,探究其产生原因及解决方法,为生产线的稳定运行提供技术支持和解决