
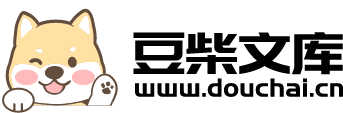
曲面5轴数控加工进给速度误差自动补偿方法.docx
快乐****蜜蜂
在线预览结束,喜欢就下载吧,查找使用更方便
相关资料
曲面5轴数控加工进给速度误差自动补偿方法.pptx
汇报人:目录PARTONEPARTTWO背景介绍补偿方法的重要性补偿方法的原理PARTTHREE加工过程中的误差来源进给速度对加工精度的影响误差传递与累积PARTFOUR数据采集与处理误差模型建立与验证补偿算法设计与实现补偿效果评估与优化PARTFIVE应用场景分析与传统方法的比较优势对加工精度和效率的提升PARTSIX实际应用案例介绍补偿效果的实际验证用户反馈与评价PARTSEVEN技术发展趋势与挑战未来研究方向与展望THANKYOU
曲面5轴数控加工进给速度误差自动补偿方法.docx
曲面5轴数控加工进给速度误差自动补偿方法曲面5轴数控加工进给速度误差自动补偿方法摘要:随着制造业领域对曲面加工精度要求的提高,由于机床本身的结构刚性等因素,使得曲面数控加工过程中加工速度误差进一步放大。针对这一问题,本文提出了曲面5轴数控加工进给速度误差自动补偿方法。通过分析加工过程中的误差来源和数控系统的结构特点,采用改进的运动规划算法,并结合曲面误差补偿方法,实现了进给速度误差的自动补偿,提高了加工精度和加工效率。关键词:曲面加工,5轴数控加工,进给速度误差,自动补偿,加工精度,加工效率1.引言随着现
加工进给速度优化的刀轨曲线轮廓误差补偿方法.pdf
本发明进给速度优化的刀轨曲线轮廓误差补偿方法属于复杂曲面零件高质高效加工领域,涉及一种包含进给速度优化和刀位点修改的刀轨曲线轮廓误差补偿方法。该方法根据直线插补加工代码中的刀位点和加工进给速度信息,以数控机床进给轴加速度和加加速度极限为约束,对进给速度进行优化;利用三次B样条拟合方法平滑进给速度曲线,得到最终优化后的加工进给速度;再利用刀位点和优化后进给速度,计算各轴轮廓误差补偿量,进而获得补偿后直线插补数控指令,用于实际加工,从而提高轮廓精度。该方法的实施过程仅需要修改直线插补加工代码中的刀位点和加工进
数控机床空心丝杠进给轴热误差补偿研究.pptx
汇报人:目录PARTONEPARTTWO热误差产生的原因热误差对数控机床的影响热误差补偿的必要性PARTTHREE热误差补偿方法分类基于温度监测的热误差补偿技术基于数学模型的预测补偿技术基于人工智能的智能补偿技术PARTFOUR实验设备与实验条件实验目的:研究空心丝杠进给轴热误差补偿方法实验设备:数控机床、空心丝杠、温度传感器、数据采集系统等实验步骤:a.设定实验条件,包括温度、湿度、负载等b.测量空心丝杠在不同温度下的热误差c.采用不同的补偿方法进行实验,如温度补偿、位移补偿等d.分析实验数据,得出最优
数控机床空心丝杠进给轴热误差补偿研究.docx
数控机床空心丝杠进给轴热误差补偿研究数控机床空心丝杠进给轴热误差补偿摘要:本论文针对数控机床空心丝杠进给轴在工作过程中产生的热误差问题进行深入研究。首先分析了空心丝杠进给轴的工作原理,紧接着讨论了其热误差的成因以及对机床精度产生的影响。基于此,提出了一种热误差补偿方法,包括热稳定性改进、热误差模型建立和热误差补偿系统设计。通过实验验证,该补偿方法能有效地降低机床的热误差,提高加工精度,具有一定的应用价值。关键词:数控机床;空心丝杠进给轴;热误差;补偿1.引言数控机床作为现代制造行业中不可或缺的设备,广泛应