
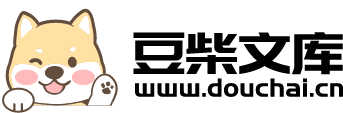
多孔介质气体润滑轴承气热耦合研究.docx
快乐****蜜蜂
在线预览结束,喜欢就下载吧,查找使用更方便
相关资料
多孔介质气体润滑轴承气热耦合研究.docx
多孔介质气体润滑轴承气热耦合研究多孔介质气体润滑轴承气热耦合研究摘要:气体润滑轴承是一种常见的摩擦副解决方案,其具有低摩擦、低噪音、无需润滑剂等优点,广泛应用于工业和机械领域。而在多孔介质气体润滑轴承中,气体与固体多孔结构的相互作用是一个重要的研究内容。本文以多孔介质气体润滑轴承气热耦合问题为研究对象,系统地探讨了气体流动和热传导在气体润滑轴承中的相互关系及其对轴承性能的影响。1.引言多孔介质气体润滑轴承是一种重要的摩擦副解决方案,在现代工业和机械领域得到广泛应用。气体润滑轴承具有高速运转、低摩擦、低噪音
石墨多孔介质气体轴承研究综述.docx
石墨多孔介质气体轴承研究综述石墨多孔介质气体轴承是目前应用广泛的一种高速无油气体轴承,具有摩擦小、摩擦系数稳定、寿命长等优点,广泛应用于高速机械设备中。本文将综述石墨多孔介质气体轴承的研究现状和发展趋势。一、石墨多孔介质气体轴承的基本原理石墨多孔介质气体轴承是利用气体在石墨多孔介质中的润滑特性来实现轴承的支撑和减摩的。石墨多孔介质材料中具有很多小气孔,气体通过这些气孔进入轴承,形成气膜,使轴承与轴之间形成气体润滑薄膜,从而达到减小摩擦系数和摩擦损失的效果。二、石墨多孔介质气体轴承的研究现状1.石墨多孔介质
多孔介质气体轴承静动态特性研究.docx
多孔介质气体轴承静动态特性研究多孔介质气体轴承静动态特性研究摘要:本文主要研究了多孔介质气体轴承的静态和动态特性。首先介绍了多孔介质气体轴承的基本原理和结构,然后分别从静态和动态两个方面对其特性进行了研究。在静态特性方面,本文重点讨论了多孔介质气体轴承的支撑力和刚度特性,包括支撑力的计算方法、刚度参数的影响因素等。在动态特性方面,主要研究了多孔介质气体轴承的振动特性和动态响应,分析了转子振动频率、阻尼比等对系统动态特性的影响。最后,通过实验验证了以上理论分析结果,说明了多孔介质气体轴承在工程实践中的应用前
气体润滑轴承的研究与发展.docx
气体润滑轴承的研究与发展气体润滑轴承是一种采用气体作为润滑介质的轴承,具有低摩擦、高精度和高运行稳定性的特点。近年来,随着工业技术的不断发展和新材料的应用,气体润滑轴承在各个领域得到了广泛应用,并在轴承技术中取得了重要的突破。本文将探讨气体润滑轴承的研究与发展,并对其未来的发展方向进行展望。首先,气体润滑轴承相较于传统的润滑轴承具有许多优势。首先,气体润滑轴承具有低摩擦和低磨损的特点。由于气体的稀薄性和流动性,气体润滑轴承大大减少了轴承内部的摩擦和磨损,从而延长了轴承的使用寿命。其次,气体润滑轴承的摩擦系
仓储内生物质多孔介质呼吸过程热湿耦合特性研究.doc
仓储内生物质多孔介质呼吸过程热湿耦合特性研究国家的发展以及人们的生产和生活离不开粮食,粮食安全储藏十分重要。粮仓本身又可以看作小型生态群落,里面包含害虫、霉菌、微生物的生存、繁殖以及仓外外部环境、仓内粮堆的呼吸作用以及粮堆的吸湿解吸湿特性共同决定。当仓外外部环境过高,粮仓水蒸气含量上升,会致使粮食颗粒呼吸作用加快,致使粮堆局部区域温湿度上升,导致害虫、霉菌大量繁殖,损害粮食品质。为保证粮食的安全储藏,可以先控制好空气介质的温度和湿度,然后通过通风的方式对粮堆的温度和水分进行控制。本文研究了通风过程中粮堆传