
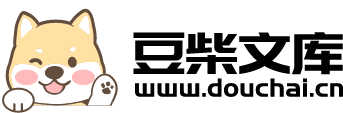
铜锗合金的深过冷、枝晶生长速率及晶粒细化研究.docx
快乐****蜜蜂
在线预览结束,喜欢就下载吧,查找使用更方便
相关资料
铜锗合金的深过冷、枝晶生长速率及晶粒细化研究.docx
铜锗合金的深过冷、枝晶生长速率及晶粒细化研究铜锗合金的深过冷、枝晶生长速率及晶粒细化研究摘要:铜锗合金是一种重要的结构材料,其深过冷性能、枝晶生长速率以及晶粒细化行为对于合金的力学性能和物理性能具有重要影响。本文通过文献调研和实验研究,综述了铜锗合金的深过冷性能、枝晶生长速率以及晶粒细化行为的研究现状和发展趋势。研究发现,在深过冷状态下,铜锗合金形成背离熔点的过饱和状态,促进了无序团簇的形成,从而抑制晶核形成,深过冷度越高,过饱和度越大,无序团簇的尺寸越大;在晶核形成之后,合金的枝晶生长速率随着过饱和度的
铜、镍及其合金深过冷熔体中的枝晶生长速率测定的开题报告.docx
铜、镍及其合金深过冷熔体中的枝晶生长速率测定的开题报告一、研究背景和意义深过冷熔体是指晶体生长温度以下的液态物质。深过冷熔体中的物质具有高过冷度和强过冷性,可以产生超饱和状态,导致枝晶生长速率急剧增加,甚至可以突破其平衡浓度,产生其他相。因此,深过冷熔体中的结晶行为具有很高的复杂性和不确定性,特别是在铜、镍及其合金中的深过冷熔体中,枝晶生长速率的测定较为困难。铜、镍及其合金是重要的化工、电子、航空、航天等行业的基础材料,它们的结构和性质与枝晶生长的方式密切相关。因此,对于铜、镍及其合金深过冷熔体中的枝晶生
铜、镍及其合金深过冷熔体中的枝晶生长速率测定的任务书.docx
铜、镍及其合金深过冷熔体中的枝晶生长速率测定的任务书任务书任务名称:铜、镍及其合金深过冷熔体中的枝晶生长速率测定任务背景:枝晶生长速率是一种重要的材料学参数,对于合金的力学性能、电学性能、热学性能等都会有着重大的影响。然而,深过冷熔体中的枝晶生长速率的研究一直比较困难。铜、镍及其合金是重要的工程材料,因此,对于这些材料在深过冷熔体中的枝晶生长速率的研究具有重要的意义。任务目标:本任务计划研究铜、镍及其合金在深过冷熔体中的枝晶生长速率,并探讨其与温度、合金成分等因素的关系。任务内容:1.实验设计:根据已有文
铜锗包晶合金深过冷熔体中的相选择研究的任务书.docx
铜锗包晶合金深过冷熔体中的相选择研究的任务书任务书题目:铜锗包晶合金深过冷熔体中的相选择研究一、研究背景与意义铜锗包晶合金是一种具有广泛应用前景的热电材料,在热电转换器中具有优异的性能。热电性能的优良主要由铜和锗之间的晶格匹配产生的包晶相效应所致。其中,包晶相由两种晶体相构成,即铜-锗尖晶石和锗-铜尖晶石。在合金加工过程中,熔体的凝固过程中晶体生长方式会直接影响包晶合金的晶体结构和性能。目前,对于铜锗包晶合金的深过冷熔体中的相选择研究还比较薄弱,缺乏深入的探索和分析,因此,本课题的研究具有重要的理论和应用
各向异性强度对过冷NiCu合金枝晶生长的影响研究.docx
各向异性强度对过冷NiCu合金枝晶生长的影响研究摘要本文研究了各向异性强度对过冷NiCu合金枝晶生长的影响,结果表明,NiCu合金在不同的各向异性强度下,枝晶生长速率有较大幅度的变化。其中,当各向异性强度较小时,枝晶生长速率大大提高,而各向异性强度越大,则枝晶生长速率越慢。这一研究结果,有助于深入理解过冷合金的枝晶形态建立机制,并为合金结构设计提供了指导。关键词:各向异性强度;过冷合金;枝晶生长;结构设计。AbstractThispaperstudiestheeffectsofanisotropystre