
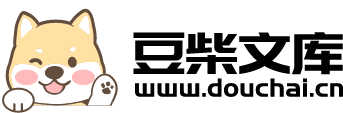
钻孔动力头钻削刀具磨损监测方法研究.docx
快乐****蜜蜂
在线预览结束,喜欢就下载吧,查找使用更方便
相关资料
钻孔动力头钻削刀具磨损监测方法研究.docx
钻孔动力头钻削刀具磨损监测方法研究钻孔动力头是一种广泛应用于地下工程中的工具,主要用于地下钻孔作业。而钻削刀具是钻孔动力头的核心部件,其磨损情况直接影响到钻孔工艺和效率。因此,对钻削刀具磨损的监测方法进行研究具有重要的理论和实际应用价值。一、研究背景与现状随着地下工程的广泛开展和需求的增加,钻削工艺和设备也逐渐得到了改进和提高。然而,在钻削过程中,由于地层复杂性和地下工程环境的特殊性,钻削刀具容易受到磨损和损坏。目前,对钻削刀具磨损的监测方法研究主要有以下几个方向:1.参数监测法:通过监测钻削过程中的力、
BTA深孔钻削刀具磨损与排屑状态监测技术研究.docx
BTA深孔钻削刀具磨损与排屑状态监测技术研究摘要本文主要研究了BTA深孔钻削刀具磨损与排屑状态监测技术,通过对BTA深孔钻削过程中钻头的磨损与排屑状态进行实时监测,可以提高生产效率,减少停机维修时间,降低生产成本,提高产品质量,具有广泛的应用前景。通过对监测方法、监测设备等方面的详细介绍,而且给出了该技术的优点与未来的发展等方面的分析。关键词:BTA深孔钻削、磨损监测、排屑状态监测、生产效率、产品质量AbstractThispapermainlystudiesthemonitoringtechnology
钻削硬岩层PDC刀具磨损分析.docx
钻削硬岩层PDC刀具磨损分析钻削硬岩层PDC刀具磨损分析摘要:随着石油勘探领域的发展,对于钻井技术的要求也越来越高,其中一项重要的工具便是PDC(聚晶立方氮化硼)刀具。然而,PDC刀具在钻削硬岩层时容易出现磨损,影响钻井效率。本文将对钻削硬岩层中PDC刀具的磨损进行分析,探讨其原因和解决方案。1.引言1.1研究背景随着世界各地石油资源的逐渐枯竭,勘探难度也越来越大。其中,钻削硬岩层是一个具有挑战性的任务,传统的钻井工具往往无法满足要求。而PDC刀具以其优异的性能,成为了钻井硬岩层的首选工具。然而,PDC刀
BTA深孔钻削刀具磨损与排屑状态监测技术研究的开题报告.docx
BTA深孔钻削刀具磨损与排屑状态监测技术研究的开题报告一、课题背景深孔加工是一种特殊的加工方式,其加工长度超过其直径之10倍以上,对工件的精度、表面质量要求极高。其中,深孔钻削作为深孔加工的主要方法,其刀具的磨损及排屑等问题关乎着加工质量和效率。因此,深入研究深孔钻削刀具磨损和排屑状态监测技术,对于提高深孔加工的效率和品质具有重要意义。二、研究内容本研究选择BTA深孔钻削刀具,采用光纤传感器等相关技术,对刀具磨损状态和排屑状态进行实时监测。主要研究内容包括:1.BTA深孔钻削刀具的磨损评价方法的研究,包括
双向钻削动力头.pdf
本发明提供了一种双向钻削动力头,属于钻削设备技术领域。包括立柱、主轴箱、摆转机构、用于安装钻头的主轴、蜗轮、蜗杆、用于驱动主轴沿其轴线方向直线移动的主轴直线进给机构及用于驱动主轴旋转的主轴旋转驱动机构,主轴箱设置在立柱上方且通过旋转轴与立柱旋转连接;摆转机构用于驱动主轴箱绕旋转轴90度摆转并锁紧;蜗轮用于驱动主轴旋转进行钻进,蜗轮套设在主轴外侧且与固设在旋转轴上的蜗杆啮合,蜗杆与旋转轴共轴线,沿主轴的轴线方向,主轴与蜗轮滑动配合。本发明提供的双向钻削动力头,适用于武装战车内部狭小空间中钻削水平向和铅垂向两