
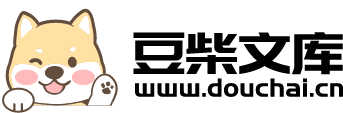
电炉炼钢工艺培训课件.ppt
lj****88
亲,该文档总共168页,到这已经超出免费预览范围,如果喜欢就直接下载吧~
相关资料
电炉炼钢工艺培训课件.ppt
电炉炼钢工艺培训课件1电炉炼钢工艺的发展历程世界电炉生产迅速发展动力我国钢铁行业2010年能耗构成的预测值,矿石经高炉/转炉流程而成粗钢的单位能耗高于600kgce/t,其中氧气转炉炼钢工序能耗仅为10kgce/t,主要能耗是高炉和炼焦工序。铁前系统烧结、炼焦和高炉炼铁是能耗大户,也是污染环境的大户。相比之下,废钢经电炉熔炼所生产的粗钢吨钢能耗仅为270kgce/t,而污染的产生及其治理更远优于高炉/转炉流程。世界粗钢产量增长情况世界钢产量预测电弧炉技术的发展2电炉炼钢主体设备介绍机械设备电气设备3电炉炼
电炉炼钢工艺课件.ppt
电炉炼钢工艺课件1电炉炼钢工艺的发展历程世界电炉生产迅速发展动力我国钢铁行业2010年能耗构成的预测值,矿石经高炉/转炉流程而成粗钢的单位能耗高于600kgce/t,其中氧气转炉炼钢工序能耗仅为10kgce/t,主要能耗是高炉和炼焦工序。铁前系统烧结、炼焦和高炉炼铁是能耗大户,也是污染环境的大户。相比之下,废钢经电炉熔炼所生产的粗钢吨钢能耗仅为270kgce/t,而污染的产生及其治理更远优于高炉/转炉流程。世界粗钢产量增长情况世界钢产量预测电弧炉技术的发展2电炉炼钢主体设备介绍机械设备电气设备3电炉炼钢的
电炉炼钢工艺.ppt
电炉炼钢工艺1电炉炼钢工艺的发展历程世界电炉生产迅速发展动力我国钢铁行业2010年能耗构成的预测值,矿石经高炉/转炉流程而成粗钢的单位能耗高于600kgce/t,其中氧气转炉炼钢工序能耗仅为10kgce/t,主要能耗是高炉和炼焦工序。铁前系统烧结、炼焦和高炉炼铁是能耗大户,也是污染环境的大户。相比之下,废钢经电炉熔炼所生产的粗钢吨钢能耗仅为270kgce/t,而污染的产生及其治理更远优于高炉/转炉流程。世界粗钢产量增长情况世界钢产量预测电弧炉技术的发展2电炉炼钢主体设备介绍机械设备电气设备3电炉炼钢的能量
电炉炼钢工艺.pptx
电炉炼钢工艺1电炉炼钢工艺的发展历程世界电炉生产迅速发展动力我国钢铁行业2010年能耗构成的预测值,矿石经高炉/转炉流程而成粗钢的单位能耗高于600kgce/t,其中氧气转炉炼钢工序能耗仅为10kgce/t,主要能耗是高炉和炼焦工序。铁前系统烧结、炼焦和高炉炼铁是能耗大户,也是污染环境的大户。相比之下,废钢经电炉熔炼所生产的粗钢吨钢能耗仅为270kgce/t,而污染的产生及其治理更远优于高炉/转炉流程。世界粗钢产量增长情况世界钢产量预测电弧炉技术的发展2电炉炼钢主体设备介绍机械设备电气设备3电炉炼钢的能量
电炉炼钢工艺.ppt
电炉炼钢工艺1电炉炼钢工艺的发展历程世界电炉生产迅速发展动力我国钢铁行业2010年能耗构成的预测值矿石经高炉/转炉流程而成粗钢的单位能耗高于600kgce/t其中氧气转炉炼钢工序能耗仅为10kgce/t主要能耗是高炉和炼焦工序。铁前系统烧结、炼焦和高炉炼铁是能耗大户也是污染环境的大户。相比之下废钢经电炉熔炼所生产的粗钢吨钢能耗仅为270kgce/t而污染的产生及其治理更远优于高炉/转炉流程。世界粗钢产量增长情况世界钢产量预测电弧炉技术的发展2电炉炼钢主体设备介绍机械设备电气设备3电炉