
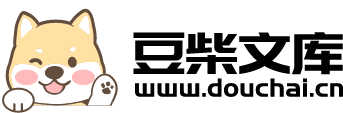
深亚微米工艺片内偏差建模方法研究与分析.docx
快乐****蜜蜂
在线预览结束,喜欢就下载吧,查找使用更方便
相关资料
深亚微米工艺片内偏差建模方法研究与分析.docx
深亚微米工艺片内偏差建模方法研究与分析研究与分析深亚微米工艺片内偏差建模方法摘要:深亚微米工艺是当前集成电路制造技术的主流,但其中存在着片内偏差的影响。为了有效地解决这一问题,本文对深亚微米工艺片内偏差建模方法进行了研究与分析。首先,介绍了深亚微米工艺的特点及片内偏差的定义和影响。接着,综述了几种常见的片内偏差建模方法,并进行了比较分析。最后,提出了一种新的基于机器学习的片内偏差建模方法,并对其进行了验证和评估。结果表明,该方法能够有效地建立深亚微米工艺片内偏差的模型,为工艺优化和产品质量提升提供了有力的
深亚微米工艺片内偏差建模方法研究与分析的任务书.docx
深亚微米工艺片内偏差建模方法研究与分析的任务书任务书一、任务背景随着微电子技术的发展和应用,深亚微米工艺成为当前半导体制造业的主流工艺之一,其逐渐成为了半导体器件制造的主流技术。而在深亚微米工艺片制造过程中,由于复杂的加工工艺和各种误差的影响,片内偏差已经成为制约制造过程精度的主要因素之一。今后的研究和应用中,如何对深亚微米工艺片内偏差进行建模和分析,加强对偏差控制的研究与分析,将成为半导体制造业实现持续改进的关键技术之一。二、任务目标本次任务的目标是研究深亚微米工艺片内偏差的建模方法与分析技术,力求在探
微米、亚微米及深亚微米CMOS工艺技术研究.docx
微米、亚微米及深亚微米CMOS工艺技术研究微米、亚微米及深亚微米CMOS工艺技术研究摘要:随着集成电路技术的不断发展,微米、亚微米及深亚微米CMOS工艺技术逐渐成为研究的热点。本论文主要对微米、亚微米及深亚微米CMOS工艺技术进行了综述和分析。首先,论文介绍了微米、亚微米及深亚微米CMOS工艺技术的背景和意义。然后,论文重点介绍了微米、亚微米及深亚微米CMOS工艺技术的发展历程和目前的研究进展。最后,论文对微米、亚微米及深亚微米CMOS工艺技术的挑战和前景进行了展望。关键词:微米、亚微米、深亚微米、CMO
超深亚微米PMOSFET的NBTI效应的研究与建模.docx
超深亚微米PMOSFET的NBTI效应的研究与建模超深亚微米PMOSFET的NBTI效应的研究与建模摘要:硅基PMOSFET已经成为现代集成电路的重要组成部分。然而,随着器件尺寸的不断缩小和工作电压的下降,器件的可靠性越来越差。其中一种主要的可靠性问题是负温度漂移效应(NBTI),它会导致器件的丢失和漏电。本文主要介绍了超深亚微米PMOSFET的NBTI效应的研究与建模。我们首先介绍了NBTI效应的基本原理,然后探讨了超深亚微米PMOSFET的器件结构和性能。接着,我们介绍了实验和建模方法,以研究NBTI
深亚微米高压集成电路中LDMOS的建模与工艺集成.docx
深亚微米高压集成电路中LDMOS的建模与工艺集成摘要:本文介绍了深亚微米高压集成电路中LDMOS的建模和工艺集成。LDMOS是一种常用的高压器件,可用于工业、医疗和航空等领域,本文通过对LDMOS原理的介绍,探讨了其建模的过程和所需的参数。同时,本文还分析了LDMOS的工艺集成,探讨了不同材料和工艺对器件特性的影响,为LDMOS的优化设计提供了理论基础。关键词:LDMOS,建模,工艺集成,参数,材料。引言:LDMOS是一种普遍应用于高压晶体管中的半导体器件,因其具有结构简单、低电阻、大功率承受能力等优点,