
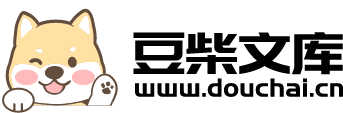
基于混合算法的车间布局多目标优化及仿真研究.docx
快乐****蜜蜂
在线预览结束,喜欢就下载吧,查找使用更方便
相关资料
基于混合算法的车间布局多目标优化及仿真研究.docx
基于混合算法的车间布局多目标优化及仿真研究基于混合算法的车间布局多目标优化及仿真研究摘要:车间布局是生产系统中的重要问题,通过合理的布局能够提高生产效率、降低成本并提高产品质量。然而,车间布局的优化是一个复杂的多目标优化问题,需要考虑多个冲突的目标指标。为了解决车间布局的多目标优化问题,本研究提出了一种基于混合算法的优化方法,并通过仿真实验进行验证。实验结果表明,基于混合算法的方法能够有效地解决车间布局的多目标优化问题,为生产系统提供了良好的布局方案。关键词:车间布局;多目标优化;混合算法;仿真1.引言车
基于混合算法的车间布局多目标优化及仿真研究的开题报告.docx
基于混合算法的车间布局多目标优化及仿真研究的开题报告一、选题背景与意义车间布局是生产系统设计中的重要组成部分,直接影响工作效率和产品质量。如何通过合理的布局设计,提高生产效率,降低成本,是制造企业所关注的重点问题之一。车间布局问题属于NP难题,优化方法多种多样,但要获得最优解仍然很难。因此,如何综合考虑多个指标进行车间布局多目标优化是一个值得研究的课题。目前已经有许多学者开展了车间布局优化研究,其中以基于混合算法的研究为主,如遗传算法、蚁群算法、粒子群算法等。这些方法通过模拟物种进化、蚁群行为、鸟群飞行等
基于混合算法的车间布局多目标优化及仿真研究的任务书.docx
基于混合算法的车间布局多目标优化及仿真研究的任务书一、研究背景车间布局是制造企业生产系统中的一个重要环节,其布局的合理性可以有效提高生产效率、优化生产流程、降低制造成本。根据车间布局不同的优化目标,车间布局问题可以归纳为单目标优化问题和多目标优化问题。传统的车间布局优化算法大多是单目标优化算法,忽略了多个目标之间的关联。因此,在实际应用中需要综合考虑多个目标,并利用多目标优化算法对车间布局进行优化。混合算法是指将多种算法组合使用的优化方法。混合算法能够充分利用各种算法的优势,提高算法的效率和准确性。近年来
基于改进遗传算法的多目标车间布局优化问题研究.docx
基于改进遗传算法的多目标车间布局优化问题研究摘要:本文研究了多目标车间布局优化问题,并提出了一种基于改进遗传算法的解决方式。本文首先介绍了车间布局优化问题的背景和意义,接着介绍了目前常用的优化方法,其中包括遗传算法。然后,本文提出了改进遗传算法的具体实现方法,包括多目标适应度函数的设计、交叉操作和变异操作的改进等。最后,本文以一个实例为例,对所提出的算法进行了测试和分析,结果表明,改进后的遗传算法可以得到更优的车间布局方案,且具有较好的稳定性和可行性。关键词:多目标优化;车间布局;遗传算法;多目标适应度函
基于混合算法的车间设备布局优化.pptx
基于混合算法的车间设备布局优化目录添加章节标题混合算法概述混合算法的定义和原理混合算法在设备布局优化中的重要性常见的混合算法类型车间设备布局优化的目标和原则设备布局优化的目标设备布局优化的原则设备布局优化的影响因素基于混合算法的车间设备布局优化方法混合算法在设备布局优化中的应用混合算法的实现步骤和流程混合算法的优化效果评估车间设备布局优化案例分析案例选择标准和来源案例的背景和现状分析案例的优化过程和实施方案案例的优化效果评估和结论未来研究方向和展望基于混合算法的车间设备布局优化的局限性未来研究的方向和重点