
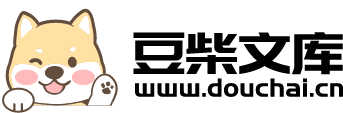
基于eM-Plant的板件柔性制造系统仿真与优化.docx
快乐****蜜蜂
在线预览结束,喜欢就下载吧,查找使用更方便
相关资料
基于eM-Plant的板件柔性制造系统仿真与优化.docx
基于eM-Plant的板件柔性制造系统仿真与优化摘要:本文针对板件柔性制造系统,结合eM-Plant仿真软件,分析了板件柔性制造系统的工作流程并建立动态模型。对模型进行了参数设置与计算,并调整系统参数进行优化,最终得到了一组优化方案。通过对比实验结果,验证了优化方案的有效性。关键词:板件柔性制造系统;eM-Plant仿真软件;动态模型;优化方案一、引言随着工业化的推进,制造行业也在不断进步。越来越多的制造企业开始将自动化技术引入生产流程中,以提高生产效率、缩短制造周期、减少生产成本并提高产品质量。板件柔性
基于eM-Plant的板件柔性制造系统仿真与优化的综述报告.docx
基于eM-Plant的板件柔性制造系统仿真与优化的综述报告介绍:板件柔性制造系统是一种用于生产制造板件的现代化生产模式,通常包括加工中心、传送带、机器人和控制系统等多种设备。为了提高生产制造的效率和质量,研究人员将仿真技术与板件柔性制造系统相结合,提出了一种新兴的仿真技术,即基于eM-Plant的板件柔性制造系统仿真。本文将对该技术进行综述,探讨其优点和应用领域。技术原理:基于eM-Plant的板件柔性制造系统仿真技术主要基于离散事件仿真(DES)技术,系统模拟每一个离散的动作来描述整个板件制造过程。在这
eMPlant生产系统仿真软件功能介绍.doc
eM-Plant生产系统仿真软件功能介绍eM-Plant是用C++实现的关于生产、物流和工程的仿真软件。它是面向对象的、图形化的、集成的建模、仿真工具,系统结构和实施都满足面向对象的要求。eM-Plant可以对各种规模的工厂和生产线,包括大规模的跨国企业,建模、仿真和优化生产系统,分析和优化生产布局、资源利用率、产能和效率、物流和供需链,以便于承接不同大小的订单与混和产品的生产。它使用面向对象的技术和可以自定义的目标库来创建具有良好结构的层次化仿真模型,这种模型包括供应链、生产资源、控制策略、生产过程、商
基于FPGA的图像开发板硬件优化设计及仿真.docx
基于FPGA的图像开发板硬件优化设计及仿真本论文主要研究基于FPGA的图像开发板的硬件优化设计及仿真。本研究的主要目标是在保证图像质量的情况下,优化图像处理开发板的性能、速度和功耗,以满足现代社会对图像处理需求的不断增长。一、研究背景与意义随着计算机和通信技术的迅速发展,图像处理技术已经成为现代社会中不可或缺的一部分。因此,图像处理技术的发展需求不断增长。基于FPGA的图像开发板是一种常见的实现图像处理算法的硬件平台,可以取代传统的软件方式,在图像处理中具有越来越重要的地位。因此本论文研究基于FPGA的图
基于正交试验法的舵板缓冲吸能结构仿真与优化.pptx
汇报人:目录PARTONEPARTTWO正交试验法的基本原理正交试验法在结构仿真与优化中的应用正交试验法在舵板缓冲吸能结构仿真与优化中的重要性PARTTHREE舵板缓冲吸能结构的组成与工作原理建立舵板缓冲吸能结构的仿真模型仿真模型的验证与修正PARTFOUR正交试验的参数选择正交试验的水平选择正交试验表的生成与优化方案制定PARTFIVE仿真结果的统计分析优化方案的确定与实施优化效果的评估与验证PARTSIX基于正交试验法的舵板缓冲吸能结构仿真与优化的效果总结对未来研究的建议与展望THANKYOU