
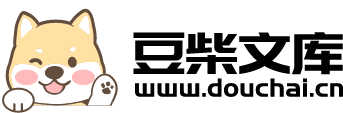
单晶硅片超精密磨削减薄技术试验研究.docx
快乐****蜜蜂
在线预览结束,喜欢就下载吧,查找使用更方便
相关资料
单晶硅片超精密磨削减薄技术试验研究.docx
单晶硅片超精密磨削减薄技术试验研究摘要:本文通过对单晶硅片超精密磨削减薄技术进行试验研究,探索了不同磨削参数对单晶硅片磨削减薄的影响,并对磨削过程中的刀具磨损、表面质量以及硅片破裂等问题进行了分析和探讨。实验结果表明,在磨削速度和磨削深度逐渐增大的情况下,单晶硅片磨削质量逐渐降低,而磨削过程中刀具磨损和热变形将会进一步加剧这一问题。因此,需要同时优化磨削参数,并对刀具进行及时更换和冷却,从而有效提高单晶硅片的磨削减薄质量和加工效率。关键词:单晶硅片;超精密磨削;磨削参数;刀具磨损;表面质量一、绪论单晶硅片
单晶硅片超精密磨削减薄技术试验研究的综述报告.docx
单晶硅片超精密磨削减薄技术试验研究的综述报告单晶硅片是半导体材料中最重要的材料之一,具有优异的电学、光学、机械和热学性能。在现代电子工业中,广泛应用于集成电路、太阳能电池和传感器等领域。而离不开单晶硅片的发展,就需要超精密磨削减薄技术的发展和应用。本文将对单晶硅片超精密磨削减薄技术试验研究进行综述。一、硅片切割加工技术硅片切割是制造集成电路基板的重要工艺环节之一,其加工质量对后续工艺影响很大。切割工艺往往也包含着磨削过程,因为切割得到的硅片,其厚度和表面粗糙度甚至在减薄前都不够理想。目前,主要的切割加工技
单晶硅片超精密磨削减薄技术试验研究的任务书.docx
单晶硅片超精密磨削减薄技术试验研究的任务书任务书一、研究背景和意义单晶硅是目前集成电路制造过程中最重要的材料之一,其亲和性、化学稳定性、高温稳定性和电学性能优异。但其制备成本高昂,特别是对于高质量、大尺寸的单晶硅片,其制备成本更为高昂。此外,单晶硅还存在一些制造上的问题,如单晶硅材料的加工硬度较高,不易加工,难以直接进行切割,而传统的加工方法如化学刻蚀法和机械磨削法的加工精度较低,造成了资源的浪费和损失。超精密磨削减薄技术是目前单晶硅制造技术的热点之一,其可以在保障加工精度和机械性能的前提下,实现对单晶硅
硅片超精密磨削减薄工艺基础研究.docx
硅片超精密磨削减薄工艺基础研究硅片超精密磨削减薄工艺基础研究摘要:随着电子技术的飞速发展,硅片作为微电子器件制造的基础材料之一,对于其加工技术的要求越来越高。其中,超精密磨削减薄工艺作为一种重要的加工方式,能够实现对硅片的高精度加工和降低其厚度,为微电子器件的封装提供了可能。本文基于硅片超精密磨削减薄工艺,进行了一系列的实验研究,探究了加工参数对加工质量的影响,并总结了硅片超精密磨削减薄工艺的基础知识和关键技术,为后续的研究和应用提供了理论和实验依据。关键词:硅片;超精密磨削减薄;加工参数;加工质量;关键
硅片超精密磨削减薄工艺基础研究的中期报告.docx
硅片超精密磨削减薄工艺基础研究的中期报告一、研究背景硅片是半导体材料的主要载体,其表面平整度和厚度精度对于光学、电学性能的影响很大。为了提高硅片加工的精度和效率,需要先将硅片进行磨削减薄处理。传统的硅片磨削减薄工艺在不断改进和优化中,但随着对硅片质量要求的提高,需要对超精密磨削减薄工艺进行进一步研究。二、研究内容本次研究旨在探究硅片超精密磨削减薄工艺的基础问题,包括轮廓磨削和平面磨削两个方面。具体研究内容如下:1.研究轮廓磨削的磨削规律和磨削机理,优化磨削参数,提高磨削效率和精度。2.研究平面磨削的表面形