
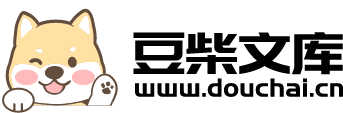
产能分析.ppt
lj****88
亲,该文档总共30页,到这已经超出免费预览范围,如果喜欢就直接下载吧~
相关资料
产能分析.ppt
产能分析培训类型:如:应会培训对象:如:生产干部和IE培训方式:如:课堂讲授培训时长:如:1H适合人数:如:60人课程目标:1.学会生产线平衡分析2.进行全厂产能分析产能分析的两个阶段产线平衡分析2.“瓶颈”的定义通常把一个流程中生产周期时间最长的环节叫做“瓶颈”(Bottleneck)。流程中存在的瓶颈不仅限制了一个流程的产出速度,而且影响了其它环节生产能力的发挥。更广义地讲,所谓瓶颈是指整个流程中制约产出的各种因素。例如,在有些情况下,可能利用的人力不足、原材料不能及时到位、某环节设备发生故障、信息流
产能分析.ppt
产能分析培训类型:如:应会培训对象:如:生产干部和IE培训方式:如:课堂讲授培训时长:如:1H适合人数:如:60人课程目标:1.学会生产线平衡分析2.进行全厂产能分析产能分析的两个阶段产线平衡分析2.“瓶颈”的定义通常把一个流程中生产周期时间最长的环节叫做“瓶颈”(Bottleneck)。流程中存在的瓶颈不仅限制了一个流程的产出速度,而且影响了其它环节生产能力的发挥。更广义地讲,所谓瓶颈是指整个流程中制约产出的各种因素。例如,在有些情况下,可能利用的人力不足、原材料不能及时到位、某环节设备发生故障、信息流
产能分析.ppt
产能分析培训类型:如:应会培训对象:如:生产干部和IE培训方式:如:课堂讲授培训时长:如:1H适合人数:如:60人课程目标:1.学会生产线平衡分析2.进行全厂产能分析产能分析的两个阶段产线平衡分析2.“瓶颈”的定义通常把一个流程中生产周期时间最长的环节叫做“瓶颈”(Bottleneck)。流程中存在的瓶颈不仅限制了一个流程的产出速度,而且影响了其它环节生产能力的发挥。更广义地讲,所谓瓶颈是指整个流程中制约产出的各种因素。例如,在有些情况下,可能利用的人力不足、原材料不能及时到位、某环节设备发生故障、信息流
产能分析、生产计划、产能均衡.ppt
产能分析、生产计划、产能均衡产能分析决定产能的三步骤一.决定毛产能假定所有印刷机每周工作7天,每天工作2班,每班10小时且没有任何停机时间,这是生产设备在完全发挥最理想的状态下的最高生产潜力。二.决定计划产能决定一周计划产能三.决定有效(可用)的产能机器生产有机器检修、保养、待料等时间,实际的工作时间达不到计划时间,且生产的产品有不良品,因此有效产能标准直接工时为1000×80%×90%=720工时产能计算练习:产能分析主要针对以下几方面人力负荷如何进行分析?机器负荷如何进行分析?10台印刷机24小时总产
产能分析、生产计划、产能均衡.ppt
产能分析、生产计划、产能均衡产能分析决定产能的三步骤一.决定毛产能假定所有印刷机每周工作7天每天工作2班每班10小时且没有任何停机时间这是生产设备在完全发挥最理想的状态下的最高生产潜力。二.决定计划产能决定一周计划产能三.决定有效(可用)的产能机器生产有机器检修、保养、待料等时间实际的工作时间达不到计划时间且生产的产品有不良品因此有效产能标准直接工时为1000×80%×90%=720工时产能计算练习:产能分析主要针对以下几方面人力负荷如何进行分析?机器负荷如何进