
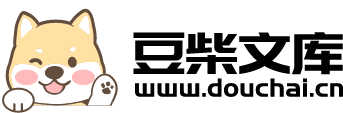
基于阳极氧化的钛合金接骨板摩擦磨损特性研究.docx
骑着****猪猪
在线预览结束,喜欢就下载吧,查找使用更方便
相关资料
基于阳极氧化的钛合金接骨板摩擦磨损特性研究.docx
基于阳极氧化的钛合金接骨板摩擦磨损特性研究摘要:本文研究了基于阳极氧化的钛合金接骨板的摩擦磨损特性。利用高分辨率扫描电子显微镜(SEM)和能量色散X射线光谱分析(EDX),研究了接骨板表面结构和元素成分的变化。利用万能试验机对接骨板进行了拉伸和弯曲试验,研究了接骨板力学性能的变化。以及运用摩擦磨损试验机研究了接骨板的摩擦磨损性能。关键词:阳极氧化;钛合金;接骨板;摩擦磨损;力学性能一、引言接骨板作为一种用于骨折固定和骨折愈合的锁定装置,已经广泛应用于临床。然而,传统的接骨板在使用过程中会产生摩擦、磨损和腐
接骨板阳极氧化装置.pdf
本发明公开了一种接骨板阳极氧化装置,包括:架体,为具有脚轮的架体;载板,水平地安装在架体下部;氧化槽,载于载板上;阴极板,固定在架体上并部分地探入到氧化槽中;升降机构,安装在架体上并位于氧化槽上方,该升降机构提供阳极通路;以及托盘,安装在升降机构输出构件的下端,以载置接骨板。依据本发明的接骨板氧化装置降低工人劳动强度,提高接骨板的表面改性质量。
TC4钛合金阳极氧化及其PTFE复合涂膜耐摩擦磨损性能研究.docx
TC4钛合金阳极氧化及其PTFE复合涂膜耐摩擦磨损性能研究摘要:TC4钛合金阳极氧化及其PTFE复合涂膜是一种新型的表面处理方法,目的是提高钛合金的耐摩擦磨损性能。本文采用了不同条件下的阳极氧化工艺,制备了不同厚度的氧化膜,接着将PTFE复合涂膜涂在阳极氧化膜上,测试其在摩擦磨损条件下的性能。结果表明,阳极氧化膜厚度对PTFE复合涂膜的附着强度有重要影响。在磨损测试中,PTFE复合涂膜能够显著地降低TC4钛合金的磨损量,并且具有较好的耐磨损性能。因此,TC4钛合金阳极氧化及其PTFE复合涂膜是一种有潜力的
钛合金摩擦磨损特性及表面改性技术研究进展.docx
钛合金摩擦磨损特性及表面改性技术研究进展摘要:钛合金是一种具有优异性能的金属材料,在航空航天、汽车、医疗器械等领域有着广泛的应用。然而,钛合金的摩擦磨损特性对其应用造成了一定的限制。本文对钛合金的摩擦磨损特性进行了综述,并对钛合金表面改性技术的研究进展进行了探讨。研究结果显示,钛合金的摩擦磨损行为主要受到材料本身性能、表面形貌、润滑条件等因素的影响。目前,研究者们通过表面改性技术,如表面涂层、表面改性合金化、沉积涂层等手段,有效地提高了钛合金的摩擦磨损性能。然而,钛合金摩擦磨损特性和表面改性技术仍然存在一
钢基铝镀层陶瓷氧化膜的摩擦磨损特性研究.docx
钢基铝镀层陶瓷氧化膜的摩擦磨损特性研究摘要:为了提高钢材的耐磨性和耐腐蚀性能,本研究使用陶瓷氧化膜对钢材表面进行涂层改性,使其具有更好的耐磨和耐腐蚀性能。通过磨损实验测试了钢基铝镀层陶瓷氧化膜的摩擦磨损特性,结果表明,涂层后的钢材摩擦系数和磨损量均得到了明显的改善,防止了钢材表面的磨损和腐蚀,具有一定的工业应用前景。关键词:钢材;氧化膜;涂层改性;摩擦磨损1.研究背景和意义钢材具有优异的力学和物理性能,广泛应用于各个领域。但随着工业化进程的不断推进,钢材的磨损和腐蚀问题也日益突出,给生产和使用带来了较大的