
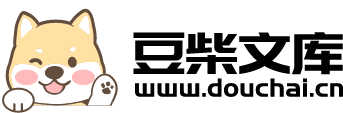
铣车复合加工中心整机热变形及误差补偿的研究.docx
快乐****蜜蜂
在线预览结束,喜欢就下载吧,查找使用更方便
相关资料
铣车复合加工中心整机热变形及误差补偿的研究.docx
铣车复合加工中心整机热变形及误差补偿的研究摘要:铣车复合加工中心在加工过程中,由于机床刚度影响、温度变化等因素的影响,会出现整机热变形现象,从而导致位置误差的产生。因此,研究整机热变形及误差补偿问题,对于提高铣车复合加工加工精度具有重要的意义。本文从整机热变形的成因和影响入手,分析误差量测技术以及常用的误差补偿方法,最后总结了目前整机热变形及误差补偿方面的研究现状和发展趋势。关键词:铣车复合加工;整机热变形;误差补偿;精度;研究现状一、引言随着科学技术的不断发展,对产品加工精度的要求也越来越高。而铣车复合
铣车复合加工中心热变形研究.docx
铣车复合加工中心热变形研究标题:铣车复合加工中心热变形研究摘要:铣车复合加工中心是一种多功能的加工设备,能够同时进行铣削和车削操作。然而,在加工过程中,由于高速切削引起的热效应,会导致机床热变形,给加工精度和工件表面质量带来不利影响。因此,对铣车复合加工中心的热变形进行研究,有助于优化加工方案,提高加工精度和效率。1.引言铣车复合加工中心是一种集铣削和车削于一体的多功能加工设备,具有高效、高精度和高自动化程度的特点。近年来,随着制造业的快速发展和对加工效率和精度要求的提高,铣车复合加工中心在各个行业得到了
铣车复合加工中心整机热特性分析研究的中期报告.docx
铣车复合加工中心整机热特性分析研究的中期报告本研究旨在针对铣车复合加工中心的整机热特性进行分析和研究。本次报告为该项研究的中期报告,主要介绍了研究进展和初步结论。一、研究进展1.研究目标和意义铣车复合加工中心是当前制造业中广泛应用的一种精密加工设备。该设备具有加工效率高、精度高、自动化程度较高等优点,但在使用过程中也存在着一些问题,其中之一就是加工过程中容易产生热量,进而影响整机的性能表现。因此,分析铣车复合加工中心的整机热特性,可以为其优化设计和生产工艺提供重要的理论和技术支持,并且有望为后续的研究提供
铣车复合加工中心热特性研究.docx
铣车复合加工中心热特性研究铣车复合加工中心热特性研究摘要:铣车复合加工中心是一种多功能和高效率的加工设备,广泛应用于制造业。然而,由于其运转时产生的高温会影响加工过程和零部件质量,因此研究铣车复合加工中心的热特性对于提高加工效率和产品质量至关重要。本文首先介绍了铣车复合加工中心的结构和工作原理,然后详细讨论了其热特性的研究方法和实验结果。最后,本文总结了铣车复合加工中心热特性的影响因素和未来的研究方向。关键词:铣车复合加工中心;热特性;加工效率;产品质量1.引言铣车复合加工中心是一种同时具备铣削和车削功能
铣车复合加工中心双驱进给系统同步热误差分析.docx
铣车复合加工中心双驱进给系统同步热误差分析铣车复合加工中心双驱进给系统同步热误差分析摘要铣车复合加工中心是一种高效、高精度的机床设备,广泛应用于航空航天、汽车制造等领域。然而,由于进给系统的热误差,该设备的加工精度可能受到一定的影响。本论文通过分析铣车复合加工中心双驱进给系统的同步热误差机理,并采用实验方法验证热误差对加工精度的影响。1.引言铣车复合加工中心是一种可以进行多种加工操作的机床设备。在实际加工过程中,进给系统的准确性和稳定性是确定加工精度的重要因素之一。然而,由于进给系统的工作过程中会产生热量