
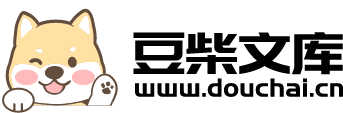
过共晶铝硅合金熔体处理及变质研究.docx
快乐****蜜蜂
在线预览结束,喜欢就下载吧,查找使用更方便
相关资料
过共晶铝硅合金熔体处理及变质研究.docx
过共晶铝硅合金熔体处理及变质研究过共晶铝硅合金熔体处理及变质研究摘要:过共晶铝硅合金是一类重要的结构材料,具有优异的综合性能。在熔体处理和变质研究中,研究人员通过调整合金的成分和工艺参数,以获得所需的结构和性能。本文综述了过共晶铝硅合金的熔体处理和变质研究,包括熔体凝固过程、过共晶相的形成机制、合金成分的优化、熔体处理的方法和工艺参数的影响。研究结果表明,合金的成分和工艺参数对熔体的凝固行为和相组成有重要影响,进而对合金的力学性能和耐腐蚀性能产生影响。未来的研究可以进一步探索熔体处理和变质的机制,以及开发
过共晶铝—硅合金变质的试验研究.docx
过共晶铝—硅合金变质的试验研究过共晶铝—硅合金变质的试验研究摘要:过共晶铝—硅合金由于其良好的高温性能和优越的力学性能,在航空航天、汽车、电子等领域得到了广泛应用。本文通过对过共晶铝—硅合金的试验研究,深入探讨了其变质行为及影响因素。实验结果表明,合金中的硅含量和变质温度是影响过共晶铝—硅合金变质的主要因素。此外,添加其他元素对过共晶铝—硅合金的变质行为也产生一定的影响。本文的研究对于深入理解过共晶铝—硅合金的变质机制以及合金的优化设计具有指导意义。关键词:过共晶铝—硅合金;变质;硅含量;变质温度;元素添
过共晶铝硅合金变质工艺研究.docx
过共晶铝硅合金变质工艺研究过共晶铝硅合金变质工艺研究摘要:过共晶铝硅合金是一种重要的结构材料,在航空、汽车等领域有广泛的应用。本论文通过对过共晶铝硅合金的研究,探讨了其变质工艺及影响因素。研究结果表明,通过合适的变质工艺可以有效提高过共晶铝硅合金的力学性能和热稳定性。本文总结了目前的研究成果,并展望了未来研究的方向。关键词:过共晶铝硅合金,变质工艺,力学性能,热稳定性引言:过共晶铝硅合金是由铝和硅组成的复合材料,其具有良好的力学性能和热稳定性,因而在航空、汽车、电子等领域有广泛的应用。过共晶铝硅合金的性能
过共晶铝硅合金的变质试验研究.docx
过共晶铝硅合金的变质试验研究过共晶铝硅合金的变质试验研究摘要:过共晶铝硅合金是一种重要的工程材料,具有良好的强度和高温耐腐蚀性能。在本文中,我们对过共晶铝硅合金进行了变质试验的研究。通过调整合金中铝和硅的含量,采用不同的变质工艺,对材料的显微组织和力学性能进行了分析。实验结果表明,适量的变质处理可以显著改善合金的强度和硬度。此外,通过观察合金的显微组织,并使用X射线衍射仪对合金的晶体结构进行了分析,以了解变质处理对合金晶界和晶体织构的影响。本文对于进一步理解过共晶铝硅合金的变质行为和优化合金的性能具有一定
A390过共晶铝硅合金变质及热处理组织、性能研究.docx
A390过共晶铝硅合金变质及热处理组织、性能研究摘要:共晶铝硅合金是一种重要的轻质材料,其组织、性能对其应用范围和可靠性有着重要影响。本文以A390共晶铝硅合金为研究对象,研究其变质及热处理后的组织、性能变化规律。结果表明,经过T6时效处理后,A390共晶铝硅合金的抗拉强度、屈服强度和伸长率都得到了显著提高,而硬度也有所增加。随着时效时间的延长,硬度和强度逐渐增加,而伸长率则会放缓下降。此外,通过热处理可以有效地消除共晶形态,并生成板状硅颗粒,从而对材料的塑性和韧性产生积极影响。本研究得出的结论对于共晶铝