
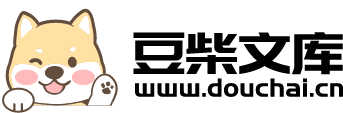
挤压膨化中气泡生长的数值模拟研究.docx
快乐****蜜蜂
在线预览结束,喜欢就下载吧,查找使用更方便
相关资料
挤压膨化中气泡生长的数值模拟研究.docx
挤压膨化中气泡生长的数值模拟研究挤压膨化中气泡生长的数值模拟研究摘要在挤压膨化过程中,气泡的生长和演化对于加工质量和材料性能至关重要。本研究采用数值模拟方法,对挤压膨化过程中气泡的生长行为进行了研究。基于流固耦合的控制方程,利用计算流体力学方法求解了气泡生长过程的动态演化。通过对不同工艺参数的数值模拟,得到了气泡生长的相关规律,并进行了相关的分析和讨论。研究结果表明,挤压膨化中气泡的生长受到多种因素的影响,如气体压力、温度变化、挤压速度等,需要综合考虑这些因素才能得到合理的生长预测。关键词:挤压膨化;气泡
挤压膨化中气泡生长的数值模拟研究的中期报告.docx
挤压膨化中气泡生长的数值模拟研究的中期报告摘要:本文旨在对挤压膨化中气泡生长的数值模拟进行中期报告。我们采用了基于体积法的数值模拟方法,并使用了流体动力学软件ANSYSFluent对挤压膨化过程进行了数值模拟。在此基础上,我们进一步研究了挤压膨化中气泡的生长情况,并探讨了影响气泡生长的因素。我们的初步结果表明,在挤压膨化过程中,气泡的大小和形状随时间的推移而发生了变化,出现了明显的生长趋势。此外,我们发现影响气泡生长的因素有很多,包括挤压速度、挤压温度、挤压介质等。特别地,我们认为挤压温度对气泡生长的影响
淀粉质食品挤压膨化过程数值模拟研究的任务书.docx
淀粉质食品挤压膨化过程数值模拟研究的任务书任务书一、研究背景淀粉质食品挤压膨化是一种广泛应用于食品加工中的工艺,可以使食品在口感、营养、稳定性等方面得到提升。在此过程中,淀粉分子受力产生流变行为并发生多种物理化学改变,因此挤压膨化过程需要深入了解其内在机制。数值模拟是一种快捷有效的研究方法,在食品加工中得到了广泛应用。因此,开展淀粉质食品挤压膨化数值模拟研究,是当前快速发展的食品加工技术领域的迫切需要。二、研究目的本项目旨在开展淀粉质食品挤压膨化过程数值模拟研究,分析挤压膨化过程中各参数之间的相互影响,探
糙米挤压膨化的研究.pdf
交错气泡运动特性数值模拟研究.docx
交错气泡运动特性数值模拟研究交错气泡运动特性数值模拟研究摘要:本文面向交错气泡运动特性进行数值模拟分析,以探究气泡在环境中的运动规律,其中涉及到气泡尺寸、浓度、环境结构等因素对气泡运动特性的影响。文章首先介绍了数值模拟方法的基本原理,接着从气泡运动特性的角度分析了影响因素,并结合数值模拟分析结果探讨了交错气泡运动特性的相关规律。最后,总结了研究成果并进行了展望。关键词:交错气泡、数值模拟、运动特性、影响因素、运动规律引言:气泡的运动特性研究具有重要的理论和应用价值。交错气泡运动特性作为气泡运动特性研究的重