
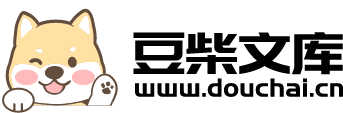
数控滚齿机几何误差建模与补偿研究.docx
快乐****蜜蜂
在线预览结束,喜欢就下载吧,查找使用更方便
相关资料
数控滚齿机几何误差建模与补偿研究.docx
数控滚齿机几何误差建模与补偿研究数控滚齿机几何误差建模与补偿研究摘要:随着社会工业化发展的需要,数控滚齿机作为高效、精确的齿轮加工设备,在汽车、航空航天等领域得到了广泛应用。然而,由于机械结构、刀具磨损、传动误差等因素的存在,数控滚齿机在加工过程中难免会出现一定的几何误差,严重影响了齿轮的质量和工作精度。因此,本文对数控滚齿机的几何误差进行建模与补偿研究,并提出了相应的解决方案。1.引言数控滚齿机是一种利用齿轮切削刀具与齿轮面滚子之间的相对运动来进行齿轮加工的机床。在实际应用中,数控滚齿机的几何误差是造成
数控滚齿机几何误差建模与分析.docx
数控滚齿机几何误差建模与分析数控滚齿机几何误差建模与分析摘要:数控滚齿机被广泛应用于齿轮制造领域,几何误差是影响其加工质量的重要因素之一。本文通过对数控滚齿机几何误差的建模与分析,揭示了误差产生的机理,为加工过程中的误差控制提供了理论依据。关键词:数控滚齿机;几何误差;建模;分析;加工质量1.引言随着工程领域对齿轮精度要求的不断提高,数控滚齿机的应用越来越广泛。然而,由于数控滚齿机自身的限制和外界因素的干扰,加工过程中难免会产生一定的几何误差。因此,对数控滚齿机几何误差的建模与分析具有重要意义。2.数控滚
数控滚齿机几何误差与热误差实时补偿技术研究.docx
数控滚齿机几何误差与热误差实时补偿技术研究随着我国制造业的不断发展和进步,数控滚齿机已经成为了生产企业中必不可少的一种设备。然而,在使用数控滚齿机进行加工时,经常会出现某些几何误差,这些误差往往会影响零件的加工精度和质量,甚至还可能会影响到整个产品的性能。因此,在数控滚齿机的应用中,如何有效地解决几何误差成为了一项重要的研究内容。而热误差是数控滚齿机几何误差的主要原因之一,因此,研究数控滚齿机的几何误差与热误差实时补偿技术,具有重要意义和现实意义。一、数控滚齿机常见的几何误差(一)基础几何误差基础几何误差
数控滚齿机几何误差与热误差实时补偿技术研究的任务书.docx
数控滚齿机几何误差与热误差实时补偿技术研究的任务书任务书一、研究背景和意义数控滚齿机是一种主要用于制造高精度齿轮的机床,其精度、效率和可靠性对于齿轮制造质量的提高及制造成本的降低具有重要意义。目前,我国的数控滚齿机技术已经走在了世界前列,但是还存在一些难题,如几何误差和热误差的影响。其中,几何误差是指由于机床制造和装配精度不足、材料热胀冷缩等原因所引起的误差;热误差是指热变形对机床精度的影响。几何误差和热误差都会导致齿轮加工精度的下降,因此,实现几何误差和热误差的实时补偿技术研究具有重要意义。二、研究内容
数控滚齿机热误差补偿技术研究.docx
数控滚齿机热误差补偿技术研究数控滚齿机热误差补偿技术研究摘要随着工业自动化程度的不断提高,数控滚齿机在齿轮加工领域的应用越来越广泛。然而,传统的数控滚齿机普遍存在热误差问题,严重影响了加工效率和加工质量。因此,研究数控滚齿机热误差补偿技术具有重要意义。本文介绍了数控滚齿机的热误差产生原因,分析了热误差对加工质量的影响,并针对不同类型的数控滚齿机,总结了热误差补偿技术的研究现状和发展趋势。关键词:数控滚齿机;热误差;补偿技术1.引言数控滚齿机是一种高精度的齿轮加工设备,在汽车、航空、机械等领域具有重要的应用