
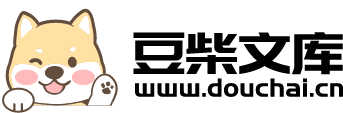
球铁的金相组织PPT课件.ppt
ca****ng
亲,该文档总共31页,到这已经超出免费预览范围,如果喜欢就直接下载吧~
相关资料
球铁的金相组织PPT课件.ppt
球墨铸铁的生产1.球铁牌号及力学性能(GB1348-88)球铁力学性能的验收依据,主要为抗拉强度(σb)和伸长率(δ),如用户有特殊需要,冲击韧性、屈服点、硬度也可作为附加的验收依据,必要时还应对金相组织进行检验。在特殊情况下,经供需双方同意,允许根据铸件本体所测得的硬度值规定球铁的硬度牌号,见GB1348-88。2.金相组织目前,可以通过各种工艺手段,在铸态获得铁素体或几乎全部为珠光体的球墨铸铁,除去了退火或正火处理,缩短生产周期,降低成本。在通常的生产条件下,由于某些化学元素的偏析以及球铁的凝固特性等
金相组织识别铁碳相图PPT课件.ppt
金相组织识别——铁碳相图金相组织识别——铁碳相图金相组织识别——铁碳相图金相组织识别——铁碳合金的基本相金相组织识别——铁碳合金的基本相金相组织识别——铁碳合金的基本相金相组织识别——珠光体727℃9金相组织识别——贝氏体金相组织识别——贝氏体金相组织识别——贝氏体金相组织识别——贝氏体金相组织识别——马氏体金相组织识别——马氏体金相组织识别——马氏体金相组织识别——马氏体金相组织识别——典型钢铁组织金相组织识别——典型钢铁组织金相组织识别——典型钢铁组织退火或者正火时,由于加热温度过高或者冷却过分缓慢会
铁碳合金相图及平衡组织分析ppt课件.ppt
铁碳合金相图及平衡组织分析Fe—Fe3C合金平衡相图铁碳合金平衡组织试样工业纯铁(4%硝酸酒精溶液)15钢(4%硝酸酒精溶液)45钢(4%硝酸酒精溶液)65钢(4%硝酸酒精溶液)T8钢(4%硝酸酒精溶液)T12钢(4%硝酸酒精溶液)T12钢(碱性苦味酸钠水溶液)共晶白口铁(4%硝酸酒精溶液)亚共晶白口铁(4%硝酸酒精溶液)过共晶白口铁(4%硝酸酒精溶液)不同含碳量的铁碳合金平衡组织形貌特征该试样共两套(20块)
铁碳合金相图详解ppt课件.ppt
铁碳合金Iron-carbonAlloy5.2铁碳合金相图分析5.2铁碳合金相图分析5.2铁碳合金相图分析5.2铁碳合金相图分析5.2铁碳合金相图分析5.2铁碳合金相图分析5.2铁碳合金相图分析5.2铁碳合金相图分析5.2铁碳合金相图分析5.2铁碳合金相图分析5.2铁碳合金相图分析5.2铁碳合金相图分析5.2铁碳合金相图分析5.2铁碳合金相图分析5.2铁碳合金相图分析5.2铁碳合金相图分析5.2铁碳合金相图分析5.2铁碳合金相图分析5.2铁碳合金相图分析5.2铁碳合金相图分析5.2铁碳合金相图分析5.2铁
铁碳合金相图分析ppt课件.ppt
第七章铁碳合金7.1概述铁碳合金可形成两个同素异构体,多种组织,性能变化范围宽;776℃以下,具有铁磁性;熔点为1538℃,热激活过程可以在不太高的温度下进行。可以有意无意地加入其它元素,得到各种各样的性能。7.2纯铁液相(L)δ-Feγ-Feα-Fe其中:δ-Fe为体心立方晶体结构。γ-Fe为面心立方晶体结构,此时发生第一次同素异形转变;γ-Fe面心立方的边长为0.36563nm,最近原子间距为0.25850nm,原子半径0.12925nm,四面体间隙的边长为0.02908nm,八面体间隙边长为0.05