
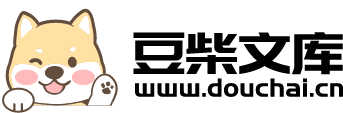
基于Dynaform纵梁后板成形工艺及回弹控制模拟分析.docx
快乐****蜜蜂
在线预览结束,喜欢就下载吧,查找使用更方便
相关资料
基于Dynaform纵梁后板成形工艺及回弹控制模拟分析.docx
基于Dynaform纵梁后板成形工艺及回弹控制模拟分析基于Dynaform纵梁后板成形工艺及回弹控制模拟分析一、引言现今整个汽车行业正处于高速发展阶段,为了满足市场需求,提高产品的竞争力,汽车制造商开始关注产品的轻量化设计,而轻量化设计的核心手段之一就是加强材料的使用,同时保证车身结构的强度和稳定性。因此,材料的成形工艺和回弹控制就成为了汽车制造过程中的关键问题。在众多成形工艺中,Dynaform成形模拟技术由于其高精度、高效率等优点,已经成为了研究汽车零部件成形过程和回弹控制的重要工具。本论文以汽车底盘
基于Dynaform纵梁后板成形工艺及回弹控制模拟分析.docx
基于Dynaform纵梁后板成形工艺及回弹控制模拟分析1.引言随着汽车工业的不断发展,车身结构材料和制造工艺不断更新换代。其中,纵梁后板是车身结构中的重要部件之一,对车身的强度和稳定性至关重要。因此,研究纵梁后板的成形工艺和回弹控制,对于提高汽车制造技术的水平具有重要的意义。Dynaform是一种广泛使用的模拟软件,利用该软件可以对车身结构的成形工艺和回弹控制进行模拟和分析。本文将运用Dynaform模拟工具,对纵梁后板的成形工艺和回弹控制进行模拟分析,以期为汽车制造技术的发展做出贡献。2.纵梁后板成形工
基于Dynaform的梁类件成形分析及回弹研究.docx
基于Dynaform的梁类件成形分析及回弹研究摘要:本文基于Dynaform模拟了梁类件成形过程,并进行了回弹分析。在成形过程中,我们使用了材料本构模型和网格优化算法,可准确地预测成形后的几何尺寸和应力分布。回弹分析中,我们考虑了材料的弹性和各向异性,最终得出了回弹量和变形量。结果表明,Dynaform是一种可靠的方法,能够帮助设计人员有效地预测成形和回弹,并优化工艺参数以减少回弹。关键词:Dynaform;梁类件成形分析;回弹研究;材料本构模型1.引言梁类件作为重要的结构部件,在航空航天、汽车、机械等领
基于Dynaform地板纵梁回弹解决方案.docx
基于Dynaform地板纵梁回弹解决方案本文将探讨基于Dynaform地板纵梁回弹解决方案的研究和应用,并从材料选择、工艺参数调整、模拟分析、实验验证等方面进行深入探讨。1.概述地板纵梁的回弹是造成汽车车身尺寸精度无法达到设计预期的主要原因之一,因此开发一套可行的地板纵梁回弹解决方案对于提升汽车车身精度至关重要。Dynaform作为现代有限元仿真软件,在解决工程设计问题方面具有不可替代的地位。本文将以Dynaform地板纵梁回弹解决方案为研究对象,深入探讨其应用和研究。2.材料选择材料选择是地板纵梁回弹解
基于DYNAFORM的边梁成形工艺分析及拉伸模设计.docx
基于DYNAFORM的边梁成形工艺分析及拉伸模设计随着汽车工业和航空工业的不断发展,对于轻量化材料和高性能材料的需求也越来越迫切。其中的一个关键技术就是边梁成形技术。边梁是一种结构较薄、兼有横向和纵向连接的工件,应用广泛,在汽车工业和航空航天工业中均有很大的需求。边梁的成形过程主要包括拉伸、冲压、弯曲等工艺。其中,拉伸工艺是边梁成形中最常见的一种工艺之一。DYNAFORM是一种常用的模拟软件,可以用来对边梁成形过程进行模拟和分析,从而设计出合理的成形工艺和模具。边梁成形的工艺流程可以分为以下几个步骤:准备