
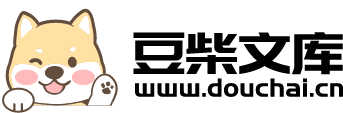
各向同性热解石墨切削机理研究.docx
快乐****蜜蜂
在线预览结束,喜欢就下载吧,查找使用更方便
相关资料
各向同性热解石墨切削机理研究.docx
各向同性热解石墨切削机理研究摘要:本文主要针对各向同性热解石墨切削机理进行了深入的研究。首先介绍了热解石墨的制备方法以及其基本结构特征。接着对其切削机理进行了详细的探究,包括切削力与表面粗糙度的关系、切削温度的分析、材料切屑的形成机理等。最后,本文总结了各向同性热解石墨切削机理的研究现状,并对其未来的发展方向进行了展望。关键词:热解石墨;切削机理;切削力;表面粗糙度;切削温度;切屑形成机理;发展方向一、引言热解石墨以其高强度、高导热性和耐高温等特点,被广泛应用于制造航空航天、电子、能源等领域的高精度零部件
各向同性热解石墨精密可切削性研究.docx
各向同性热解石墨精密可切削性研究引言各向同性热解石墨是一种重要的高性能材料,具有高强度、高刚性、高温稳定性、有良好的电导和导热性能等特点,常被用于工业和科研领域的高端应用中。其中,精密可切削性是研究各项同性热解石墨的关键特性之一,而且直接关系到材料的加工性能和使用寿命。因此,本文将从材料结构、制备工艺、加工特性等方面,系统地探讨各项同性热解石墨的精密可切削性,并提出一些有益的改进措施,以增强材料的性能和应用价值。一、各向同性热解石墨的结构特点各向同性热解石墨中,石墨晶粒是沿着晶体间隙排列的六边形结构网状物
各向同性热解石墨精密可切削性研究的任务书.docx
各向同性热解石墨精密可切削性研究的任务书任务书:一、背景热解石墨是一种高性能的非金属材料,具有机械强度高、耐腐蚀性好、导热、电性能优异等特点,在航空、航天、汽车、仪器仪表等领域都有广泛应用。而在制造热解石墨零件时,通常需要进行加工,而其可切削性能往往是影响加工效率和质量的重要因素。因此,研究热解石墨的精密可切削性能,对于提高加工效率和零件质量具有重要意义。二、研究目的本研究旨在探究各向同性热解石墨的精密可切削性能及其影响因素。具体包括以下目标:1.研究各向同性热解石墨的微观结构特征及其对可切削性能的影响。
热处理调控各向同性热解石墨微观结构及性能研究综述报告.docx
热处理调控各向同性热解石墨微观结构及性能研究综述报告热解石墨是一种在空气中高温下热解制备的材料,具有较高的比表面积和优良的导电性能,在许多领域具有广泛的应用。然而,由于其微观结构存在各向异性,导致其性能在不同方向上存在巨大差异,难以满足不同应用领域的需求。因此,热处理调控热解石墨微观结构及性能成为了研究热解石墨的重要方向之一。热处理是通过加热和冷却等操作来改变材料的物理、化学或微观结构,以满足不同应用领域的需求。对热解石墨进行热处理可以调控其微观结构,从而实现各向同性特性的控制。在热处理过程中,常见的方法
各向同性热解石墨的机械加工与密封性能研究的任务书.docx
各向同性热解石墨的机械加工与密封性能研究的任务书任务书研究题目:各向同性热解石墨的机械加工与密封性能研究研究目的和意义:热解石墨是一种具有优异的性能的材料,其强度高、耐腐蚀、导热性好等特点使其在化工、航空、电子、航天等领域得到广泛的应用。热解石墨在工业生产中常被用作密封材料。然而,其加工难度大、加工精度要求高、易出现裂缝等问题限制了其应用的进一步发展。因此,本次研究旨在研究热解石墨的机械加工及其密封性能,为其在工业生产中的应用提供技术支持。研究任务:1.热解石墨的机械加工技术研究,包括切割、车削、铣削等。