
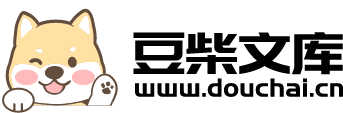
双轴载荷下表面裂纹及孔边裂纹的弹塑性分析.docx
快乐****蜜蜂
在线预览结束,喜欢就下载吧,查找使用更方便
相关资料
双轴载荷下表面裂纹及孔边裂纹的弹塑性分析.docx
双轴载荷下表面裂纹及孔边裂纹的弹塑性分析双轴载荷下表面裂纹及孔边裂纹的弹塑性分析摘要:本文通过对双轴载荷下表面裂纹及孔边裂纹的弹塑性分析,探讨了裂纹、孔洞的强度和稳定性对材料稳定性的影响,建立了裂纹、孔洞的弹塑性模型,并通过模拟分析得出了受力状态下,裂纹、孔洞主应力和剪应力随时间变化的规律。结果表明,在材料弹性极限之外,材料界面内部的弹塑性失稳导致了双轴载荷下的破裂和毁损。关键词:双轴载荷、表面裂纹、孔边裂纹、弹塑性分析、材料稳定性引言:在现代工业生产中,材料破裂和损伤是重大安全隐患之一,深入探究材料受力
反平面裂纹在裂纹自由表面附近的弹塑性分析.docx
反平面裂纹在裂纹自由表面附近的弹塑性分析反平面裂纹在裂纹自由表面附近的弹塑性分析摘要:本文以反平面裂纹在裂纹自由表面附近的弹塑性分析为研究对象,通过理论推导和数值模拟的方法,对该问题进行了深入研究。首先,介绍了裂纹的基本概念和裂纹力学理论的发展历程。然后,对反平面裂纹的特点进行分析,并推导了裂纹自由表面附近的弹塑性分析模型。最后,通过数值模拟验证了所得到的结果,并对其进行了讨论和总结。关键词:反平面裂纹;裂纹自由表面;弹塑性分析1.引言裂纹是材料中常见的一种缺陷,其存在会导致材料的强度和使用寿命大大降低。
一个双向载荷下弹塑性裂纹稳定扩展的分析方法.docx
一个双向载荷下弹塑性裂纹稳定扩展的分析方法双向载荷下弹塑性裂纹稳定扩展的分析方法裂纹是许多结构和材料中常见的缺陷之一,它们会对其强度和可靠性产生很大的影响。裂纹在双向载荷下的稳定扩展是一个重要的工程问题,因为在许多实际应用中,结构和材料都会受到来自多方向的力的作用。针对这个问题,本文将介绍一种针对双向载荷下弹塑性裂纹稳定扩展的分析方法。该方法基于线性弹性断裂力学和塑性断裂力学理论,并使用有限元方法进行数值模拟。首先,介绍线性弹性断裂力学的基本概念。在弹性阶段,应力-应变关系可以用胡克定律表示。当裂纹出现时
热载荷下圆柱表面裂纹分析.pptx
汇报人:CONTENTSPARTONEPARTTWO热载荷与裂纹产生的关系热载荷对裂纹扩展的影响热载荷对裂纹敏感性的影响热载荷对裂纹检测的影响PARTTHREE裂纹的形态特征裂纹的分布规律裂纹的深度与长度裂纹的温度梯度特性PARTFOUR材料性质对裂纹形成的影响热载荷参数对裂纹形成的影响制造工艺对裂纹形成的影响环境因素对裂纹形成的影响PARTFIVE无损检测技术应用裂纹的定量评估方法裂纹扩展速率的预测剩余寿命的预测与评估PARTSIX优化材料选择与处理改进制造工艺与设备加强生产过程监控与检测制定合理的维护
双轴载荷下含沿厚度方向贯穿裂纹平板的极限载荷分析.docx
双轴载荷下含沿厚度方向贯穿裂纹平板的极限载荷分析双轴载荷下含沿厚度方向贯穿裂纹平板的极限载荷分析引言裂纹是一个常见的问题,在许多工程结构中都会出现。在材料中出现裂纹后,会对物体的强度产生影响,甚至可能导致物体的破坏。因此,对于裂纹的分析和研究具有重要的意义。本文主要研究双轴载荷下含沿厚度方向贯穿裂纹平板的极限载荷分析。问题分析在双轴载荷下,含有裂纹的平板之间的应力分布不均匀。而对于承载结构,平板上的裂纹可能会对平板的载荷能力产生显著影响。为了分析这种影响,需要对裂纹的形态、裂纹的长度、宽度、深度等进行评估