
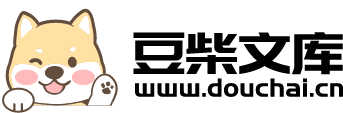
巯基苯并噻唑反应釜的理论设计.docx
13****88
亲,该文档总共123页,到这已经超出免费预览范围,如果喜欢就直接下载吧~
相关资料
巯基苯并噻唑反应釜的理论设计.docx
编号:时间:2021年x月x日书山有路勤为径,学海无涯苦作舟页码:第页共NUMPAGES123页第PAGE\*MERGEFORMAT123页共NUMPAGES\*MERGEFORMAT123页HYPERLINK""1绪论1.1工艺概述1.1.1促进剂的发展促进剂2-巯基苯并噻唑(以下简称)是一种橡胶通用型硫化促进剂,是一种淡黄色粉末或颗粒,具有令人不愉快的气味。熔点在173.0℃以上;绝对密度为1.41~1.48;难溶于水和正己烷,易溶于丙酮,可溶于乙醇,微溶于苯。2-巯基苯并噻唑
巯基苯并噻唑反应釜的理论设计.docx
1绪论1.1工艺概述1.1.1促进剂的发展促进剂2-巯基苯并噻唑(以下简称)是一种橡胶通用型硫化促进剂是一种淡黄色粉末或颗粒具有令人不愉快的气味。熔点在173.0℃以上;相对密度为1.41~1.48;难溶于水和正己烷易溶于丙酮可溶于乙醇微溶于苯。2-巯基苯并噻唑呈酸性硫化促进性强硫化曲线比较平坦且污染性小。该品低毒刺激皮肤和粘膜能引起皮炎及难以治疗的皮肤溃疡可致敏。硫化促进剂是能够加快橡胶与硫化剂反应速率的物质简称促进剂。促进剂[1]既可提高硫化速率降低硫化温度、减少硫化剂用量同时也能使硫化橡脏的物
巯基苯并噻唑反应釜的理论设计.docx
编号:时间:2021年x月x日书山有路勤为径,学海无涯苦作舟页码:第页共NUMPAGES101页第PAGE\*MERGEFORMAT101页共NUMPAGES\*MERGEFORMAT101页HYPERLINK""1绪论1.1工艺概述1.1.1促进剂的发展促进剂2-巯基苯并噻唑(以下简称)是一种橡胶通用型硫化促进剂,是一种淡黄色粉末或颗粒,具有令人不愉快的气味。熔点在173.0℃以上;相对密度为1.41~1.48;难溶于水和正己烷,易溶于丙酮,可溶于乙醇,微溶于
关于橡胶促进剂2-巯基苯并噻唑反应釜的理论设计.doc
苯胺法高压搅拌合成2-巯基苯并噻唑反应器(3m3)的设计971绪论1.1工艺概述1.1.1促进剂的发展促进剂2-巯基苯并噻唑(以下简称)是一种橡胶通用型硫化促进剂是一种淡黄色粉末或颗粒具有令人不愉快的气味。熔点在173.0℃以上;相对密度为1.41~1.48;难溶于水和正己烷易溶于丙酮可溶于乙醇微溶于苯。2-巯基苯并噻唑呈酸性硫化促进性强硫化曲线比较平坦且污染性小。该品低毒刺激皮肤和粘膜能引起皮炎及难以治疗的皮肤溃疡可致敏。硫化促进剂是能够加快橡胶与硫化剂反应速率的物质简称促进剂。促进剂[1]既可提高
关于橡胶促进剂2-巯基苯并噻唑反应釜的理论设计.docx
编号:时间:2021年x月x日书山有路勤为径学海无涯苦作舟页码:1绪论1.1工艺概述1.1.1促进剂的发展促进剂2-巯基苯并噻唑(以下简称)是一种橡胶通用型硫化促进剂是一种淡黄色粉末或颗粒具有令人不愉快的气味。熔点在173.0℃以上;相对密度为1.41~1.48;难溶于水和正己烷易溶于丙酮可溶于乙醇微溶于苯。2-巯基苯并噻唑呈酸性硫化促进性强硫化曲线比较平坦且污染性小。该品低毒刺激皮肤和粘膜能引起皮炎及难以治疗的皮肤溃疡可致敏。硫化促进剂是能够加快橡