
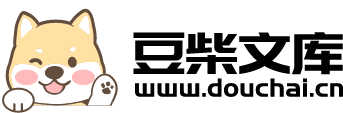
硅通孔界面损伤机理研究的开题报告.docx
快乐****蜜蜂
在线预览结束,喜欢就下载吧,查找使用更方便
相关资料
硅通孔界面损伤机理研究的开题报告.docx
硅通孔界面损伤机理研究的开题报告一、研究背景:硅通孔具有极高的电性能和可靠性,已经广泛应用于微电子学领域中。但是,在通孔制造过程中难免会伴随一些不可避免的问题,如界面损伤等。这些问题的存在往往会影响硅通孔的电性能和可靠性,甚至造成晶体管故障。因此,研究硅通孔界面损伤机理,对于提高硅通孔的制造质量和电性能具有重要的意义。二、研究目的:本研究旨在深入探究硅通孔界面损伤机理,确定其损伤发生的原因和机制,为进一步优化通孔制造工艺提供理论依据和切实可行的建议。具体研究内容包括:1.分析硅通孔界面损伤的类型和发生机制
硅通孔界面应力分析的开题报告.docx
硅通孔界面应力分析的开题报告一、研究背景随着电子设备尺寸的不断缩小和功能的不断增强,芯片的内部元器件之间的连接越来越密集,针对这种情况,硅通孔被广泛应用于芯片的制造中。硅通孔技术是通过在硅衬底上钻孔,然后将金属填充到孔内,形成的连接通道。然而,硅通孔与周围材料之间的界面应力会对芯片的可靠性和性能产生重大影响,因此,研究硅通孔界面应力是非常重要的。二、研究内容本研究旨在通过有限元方法分析硅通孔界面应力,深入探究硅通孔在芯片制造中的应用。研究内容主要包括以下几个方面:1.建立硅通孔模型并研究其特性通过建立硅通
硅通孔界面应力分析.docx
硅通孔界面应力分析硅通孔界面应力分析摘要:本文采用有限元方法对硅通孔的界面应力进行了分析。首先,对硅通孔的结构进行了简单的介绍。然后,利用ANSYS软件建立了三维模型并进行了有限元分析。最后,得出了界面应力的分布情况,并进行了讨论。关键词:硅通孔,界面应力,有限元分析,ANSYS软件引言:随着现代电子、计算机技术的飞速发展,各种微电子器件越来越复杂,同时也越来越小型化。硅通孔是一种常见的微电子器件,它具有很多的优点,如使芯片具有更高的集成度、降低信号传递延迟等。但由于硅通孔在外部环境和芯片内部直接连接,所
铜填充硅通孔在热、电条件下的微结构演化及机理研究的开题报告.docx
铜填充硅通孔在热、电条件下的微结构演化及机理研究的开题报告一、选题背景随着现代电子产品的发展,电子元器件的尺寸越来越小,通孔的直径也越来越小,同时电子产品的工作环境也越来越苛刻,要求电子产品的耐高温、耐腐蚀等性能也越来越高。针对这种需求,铜填充硅通孔被广泛应用于电子元器件的连接,用以提高电子产品的可靠性和稳定性。然而,在实际应用中,铜填充硅通孔的连接状态会受到热、电等因素的影响,从而影响其可靠性和稳定性。因此,研究铜填充硅通孔在热、电条件下的微结构演化及机理,对于提高电子元器件的可靠性和稳定性具有重要的理
钢轨的损伤机理研究的开题报告.docx
钢轨的损伤机理研究的开题报告一、选题背景铁路是一种重要的交通工具,铁路线路的安全和可靠性对国家经济发展和人民生活的安全有着重要意义。铁路线路中的核心构件之一为钢轨,而钢轨在使用过程中往往会经受各种损伤,如疲劳、腐蚀、压痕、断裂等,这些损伤不仅影响了铁路线路的安全性能,也降低了钢轨的使用寿命,因此对钢轨损伤机理的研究显得尤为重要。二、研究内容本研究在钢轨损伤机理的研究基础上,继续探索以下内容:1.钢轨损伤机理的分类,包括疲劳、腐蚀、压痕、断裂等常见损伤类型。2.对钢轨的材料和工艺进行分析,分析这些因素对钢轨