
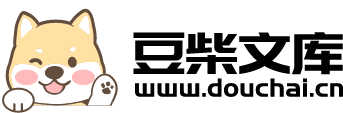
CRTSⅡ型无砟轨道轨道板厂施工改进方案.doc
sy****28
在线预览结束,喜欢就下载吧,查找使用更方便
相关资料
CRTSⅡ型无砟轨道轨道板厂施工改进方案.doc
凤阳轨道板厂施工改进方案分丝隔板与侧模间缝隙处理安装分丝隔板时,依靠模板纵向丝杆上的钩子插入插销将分丝隔板固定,由于模板使用时间过长和分丝隔板的变形,分丝隔板与模板不能紧密结合,产生了一定得缝隙,使模板下方的振捣力不能上传至分丝隔板,在轨道板混凝土浇注振捣过程中侧模严重漏浆,造成表面气泡多且缝隙较宽,轨道板两侧麻面并出现厚度不同台阶,严重影响外观质量,其处理方案如下。1、下层网片安置完毕,放置预应力钢丝后初张拉20%,安装分丝隔板并锁紧后终张拉,张拉完毕开始在用玻璃胶注入器对缝隙大于2mm的部位进行注入,
CRTSⅡ型轨道板无砟轨道施工技术手册.pdf
特别说明此资料来自豆丁网(http://www.docin.com/)您现在所看到的文档是使用下载器所生成的文档此文档的原件位于http://www.docin.com/p-98751862.html感谢您的支持抱米花http://blog.sina.com.cn/lotusbaob
CRTSⅡ型无砟轨道揭板试验施工方案.docx
杭州至宁波客运专线铁路第Ι标段专项施工方案(CRTSⅡ型无砟轨道揭板试验)编制:复核:审批:中铁三局集团五公司杭甬项目经理部二0一0年十二月目录TOC\o"1-3"\h\z\uHYPERLINK\l"_Toc281028703"一、编制依据PAGEREF_Toc281028703\h-3-HYPERLINK\l"_Toc281028704"二、工程概况PAGEREF_Toc281028704\h-3-HYPERLINK\l"_Toc281028705"三、试验目的PAGE
CRTS型无砟轨道揭板试验施工方案.doc
杭州至宁波客运专线铁路第Ι标段专题施工方案(CRTSⅡ型无砟轨道揭板试验)复核:审批:中铁三局集团五企业杭甬项目经理部二0一0年十二月目录一、编制根据-3-二、工程概况-3-三、试验目旳-4-四、资源配置-4-4.1、施工人员-4-4.2、试验仪器及设备-5-五、揭板试验使用原材料与配合比-5-六、搅拌工艺与搅拌参数旳制定-6-6.1、水泥乳化沥青砂浆产品旳生产工艺流程-6-6.2、灌注前准备工作及灌注工艺-7-七、揭板试验施工工期安排-9-八、质量、安全、文明施工及环境规定-10-8.1、施工质量保证措
第二篇无砟轨道CRTSⅡ型轨道板的施工.pptx
会计学京津城际铁路(tiělù)CRTSⅡ型无砟轨道板预制轨道板通过水泥沥青砂浆调整层,铺设在现场摊铺的混凝土支承层或现场浇筑的具有滑动层的钢筋混凝土底座(桥梁)上,适应ZPW-2000轨道电路的连续轨道板无砟轨道结构型式。包括标准板、特殊板和补偿板,标准板长6450mm、宽2550mm、厚度200mm,混凝土的设计(shèjì)强度为C55,每块板混凝土用量3.45m3,板重约8.9t,特殊板和补偿板依据具体设计(shèjì)确定。轨道板横向配置60根中¢10预应力钢筋,纵向配置6根由¢20精轧螺纹钢筋