
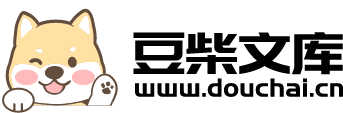
汽车覆盖件冲压成形工艺性培训讲义.ppt
天马****23
亲,该文档总共44页,到这已经超出免费预览范围,如果喜欢就直接下载吧~
相关资料
汽车覆盖件冲压成形工艺性培训讲义.ppt
21十月2024前言:好的设计是使制造变得更加容易,不需要很高的成本和精度。好的工艺是让加工更加完美,使装配变得更加容易。一次拉延成形的条件拉延件圆角R与料厚的关系拉延件的底部与壁间的R1≥t,为使拉延顺利进行,一般取R1≥(3~5)t比较规则的拉延件的凸缘与壁间的R2≥2t,为使拉延顺利进行,一般取R2≥(5~8)t,不规则的拉延件R2a≥3t,一般汽车覆盖件均为一次拉延成形因此尽可能R2a≥0.2H.此处的R3又称为凹模入口处的圆角半径.两壁间转角R3,与拉延深度有关,一般取R3≥(8~15)t,或R
汽车覆盖件冲压成形工艺.pptx
12-1汽车覆盖件冲压成形特点2-1汽车覆盖件冲压成形特点2-1汽车覆盖件冲压成形特点2-1汽车覆盖件冲压成形特点2-1汽车覆盖件冲压成形特点2-1汽车覆盖件冲压成形特点2-1汽车覆盖件冲压成形特点2-1汽车覆盖件冲压成形特点2-1汽车覆盖件冲压成形特点2-1汽车覆盖件冲压成形特点2-1汽车覆盖件冲压成形特点2-2工艺设计内容2-3工艺方案制定2-3工艺方案制定2-3工艺方案制定2-3工艺方案制定2-4汽车覆盖件模具开发流程2-4汽车覆盖件模具开发流程2-4汽车覆盖件模具开发流程2-4汽车覆盖件模具开发流
汽车覆盖件冲压工艺性的研究与应用.docx
汽车覆盖件冲压工艺性的研究与应用随着汽车制造业的不断发展,汽车覆盖件的冲压工艺性越来越重要。汽车覆盖件在汽车生产中占有至关重要的地位,而覆盖件的质量、精度和效率取决于冲压工艺的稳定性和可控性。因此,研究和应用汽车覆盖件的冲压工艺性是汽车制造业一个不可忽视的问题。首先,汽车覆盖件冲压工艺性的研究是很有必要的。规范的冲压工艺可以有效地提高汽车覆盖件的质量和精度。冲压工艺是一个需经过多次试验和实践才能得到完美的工艺流程,从而达到汽车覆盖件的标准要求。只有稳定的、高效的冲压工艺流程,才能使汽车生产企业在更短的时间
汽车覆盖件冲压成形工艺设计及软件的开发与应用概要.doc
武汉理工大学硕士学位论文汽车覆盖件冲压成形工艺设计和软件旳开发与应用姓名:王宁申请学位级别:硕士专业:材料加工工程指导教师:余世浩第1章绪论1.1选题根据和意义当今世界各国都将汽车工业列入国民经济旳支柱产业之一。伴随市场经济旳发展和全球经济二体化时代旳到来,尤其是加入WTO后来,我国旳汽车工业,尤其是轿车工业面临剧烈旳竞争和挑战,其竞争旳关键是新技术、信息化。因此,必须以高新技术来提高老式产业。衡量一种国家汽车工业,尤其是轿车工业发展水平旳重要特性是新车型旳自主开发与设计能力。伴随市场竞争加剧,对汽车产品
车身覆盖件冲压成形仿真及工艺优化.pdf
重庆大学硕士学位论文车身覆盖件冲压成形仿真及工艺优化姓名:李泽申请学位级别:硕士专业:材料加工工程指导教师:周杰;谢全清2010-04重庆大学硕士学位论文中文摘要