
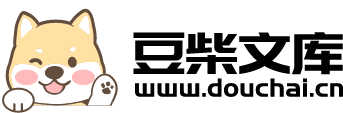
气汽混合流凝结液膜厚度分布及对换热特性的影响的综述报告.docx
快乐****蜜蜂
在线预览结束,喜欢就下载吧,查找使用更方便
相关资料
气汽混合流凝结液膜厚度分布及对换热特性的影响的综述报告.docx
气汽混合流凝结液膜厚度分布及对换热特性的影响的综述报告气汽混合流是许多工业系统中普遍存在的一种复杂的现象,如化学反应器、石化工厂、燃煤电站等。由于混合流的复杂性,许多影响换热特性的因素只能通过实验或数值模拟来研究。其中一个关键因素就是凝结液膜厚度分布。凝结液膜的形成是由于气体和水汽混合后冷却,水汽就会与气体反应而产生凝结。而液体膜的厚度通常被认为是影响传热的一个重要因素。较厚的液膜将影响传热系数、传热速率以及传热强度。因此,深入研究气汽混合流凝结液膜厚度分布及其对换热特性的影响至关重要。在实验研究中,许多
汽气混合流凝结液膜形成机理研究.docx
汽气混合流凝结液膜形成机理研究汽气混合流凝结液膜形成机理研究摘要:本文对汽气混合流凝结液膜的形成机理进行研究。通过对汽气混合流的流动特性及其对凝结液膜形成的影响进行分析,提出了汽气混合流凝结液膜形成的机理模型。同时,通过对现有实验数据的分析,验证了所提出的模型的准确性,并指出可能存在的问题并进行了讨论。关键词:汽气混合流,凝结液膜,形成机理,流动特性,模型1.研究背景在化工等工业领域中,汽气混合流凝结液膜的形成及热传导等问题一直是研究的热点问题。对于这些问题的深入研究,不仅有助于提高工业生产效率,降低生产
水平翅片管外凝结液膜分布及换热特性影响研究.docx
水平翅片管外凝结液膜分布及换热特性影响研究摘要水平翅片管作为一种常见的热交换器,在化工工业、能源领域等众多应用中发挥着重要作用。然而,随着运行时间的增加,管外凝结液膜的形成不可避免,对热交换器的换热特性产生影响。本文通过对水平翅片管管外凝结液膜的分布及其影响因素进行研究,分析了凝结液膜对热传导的影响和换热性能的变化规律,为热交换器的运行和维护提供理论支持。关键词:水平翅片管,凝结液膜,换热特性,影响因素,变化规律Introduction热交换器是常用的工业设备之一,它主要用于将一个流体的热交换给另一个流体
汽-气层流凝结气液膜内物理量分布的研究.docx
汽-气层流凝结气液膜内物理量分布的研究汽-气层流凝结是指在管道内流动的热气体与外部冷凝介质接触时发生的传热过程。在这个过程中,气体会冷凝成液体,形成气液两相流。本文将讨论在这个过程中的物理量分布,包括温度,浓度等。首先,我们来讨论温度分布。在汽-气层流凝结过程中,热气体会通过传热将热量释放给冷凝介质。在传热过程中,温度的分布是不均匀的。在接触面和凝结层内,温度较高,因为此处有较强的传热过程。随着距离凝结界面的增加,温度逐渐降低,直至达到冷凝介质的温度。这是由于传热能力与距离的平方成反比关系。因此,温度分布
水平滴型管外凝结液膜分布及换热特性研究.docx
水平滴型管外凝结液膜分布及换热特性研究水平滴型管外凝结液膜分布及换热特性研究摘要:随着工业技术的发展,传热技术的应用愈发广泛,其中液膜换热是一种重要的传热方式。本文重点研究了水平滴型管外凝结液膜的分布和换热特性,并探讨了其应用的优势和不足之处。通过实验方法,我们发现水平滴型管外凝结液膜的分布受到不同工况参数(如流速、温度、液滴大小)的影响,不同条件下液膜的分布规律存在差异。同时,我们还研究了液膜厚度和热传导系数等参数对换热效果的影响,结果表明,较薄的液膜更有利于热传导,从而提高换热效率。最后,我们总结了水