
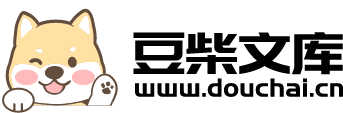
基于PCA的连续过程性能监控与故障诊断研究的综述报告.docx
快乐****蜜蜂
在线预览结束,喜欢就下载吧,查找使用更方便
相关资料
基于PCA的连续过程性能监控与故障诊断研究的综述报告.docx
基于PCA的连续过程性能监控与故障诊断研究的综述报告引言连续过程是工业自动化系统中常见的一种运行模式,例如化工、电力、制造业等领域。在生产过程中,由于存在各种外界环境因素和内在因素,连续过程可能出现运行异常或故障,这会导致生产质量和效率降低,进而导致一系列的经济损失,甚至危及人身安全。因此,实时监测和故障诊断成为连续过程运行管理的核心任务之一。基于PCA的连续过程性能监控与故障诊断方法应运而生,其核心思想是将多变量数据抽象成低维空间,在此基础上进行异常检测和故障诊断。该方法已成为拥有广泛应用的经典方法之一
基于PCA及其扩展方法的过程监控技术研究的开题报告.docx
基于PCA及其扩展方法的过程监控技术研究的开题报告一、选题的背景和意义近年来,随着现代工业化制造技术的不断发展,各种自动化生产系统在工业生产中得到广泛应用。工业生产系统存在由于设备故障、操作失误、原材料变化等因素引起的不良品率、生产效率下降等问题,对此如何有效地进行过程监控已成为一个非常重要的问题。过程监控技术是指通过对生产过程的监视实现对生产系统运行状态的把握,并及时发现引起问题的异常行为,以便采取相应的措施以减小生产风险并提高生产效率。因此,过程监控技术的应用能够帮助企业降低不良品率,减小生产成本,提
基于鲁棒PCA的化工过程故障诊断研究的任务书.docx
基于鲁棒PCA的化工过程故障诊断研究的任务书任务书一、任务背景与研究意义化工工艺是一种重要的工业生产方式,在化工生产中,过程故障是不可避免的,而有效及时地诊断故障对工业生产的保障至关重要。因此,在化工工艺中,如何实现有效快速的故障诊断,一直是研究人员关注的话题。在故障诊断领域,基于数据驱动的方法已经成为一种流行的研究方向。其中,基于主成分分析(PCA)方法的故障诊断在工业生产中得到了广泛应用。PCA方法通过将多个变量的观测值映射到少数几个互相独立的主成分上,从而实现数据降维和特征提取的目的。但是,传统的P
概率PCA多元统计方法在过程监控中的应用研究的综述报告.docx
概率PCA多元统计方法在过程监控中的应用研究的综述报告概率PCA(ProbabilisticPrincipalComponentAnalysis)是一种多元统计方法,被广泛应用于过程监控中。在过程监控中,概率PCA可用于分析和识别异常,帮助提高过程质量和保障生产安全。本文将就概率PCA多元统计方法在过程监控中的应用进行综述。概率PCA是一种基于概率模型的数据降维方法,其主要思想是利用主成分分析(PCA)将高维度数据转化为低维度数据,然后利用概率分布模型对数据进行重构。相比于传统的PCA方法,概率PCA模型
基于时间过程视角的连续并购研究综述.docx
基于时间过程视角的连续并购研究综述一、概述在当今商业环境下,企业为了追求更高的市场份额、优化资源配置或实现技术协同,纷纷采用并购这一重要战略手段。随着市场环境的快速变化,连续并购现象日益普遍,成为企业实现快速扩张和转型的关键途径。连续并购过程中涉及的时间因素、决策机制以及风险控制等问题,一直是学术界和企业界关注的焦点。基于时间过程视角的连续并购研究,旨在从时间的维度深入剖析企业连续并购的动因、过程及效果。这一研究视角强调并购活动的动态性和连续性,关注企业在不同时间节点上的并购决策、实施及整合过程,以及这些