
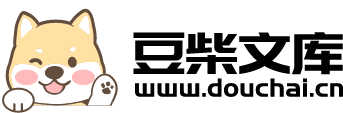
模环旋压成形过程的数值模拟与工艺优化的中期报告.docx
快乐****蜜蜂
在线预览结束,喜欢就下载吧,查找使用更方便
相关资料
模环旋压成形过程的数值模拟与工艺优化的中期报告.docx
模环旋压成形过程的数值模拟与工艺优化的中期报告中期报告一、引言模环旋压(RMS)技术是一种用于制造大规模零件的重要现代金属成形方法。在该技术中,通过在模环中组合使用压力和旋转来形成工件,可以使用低成本材料制造出高强度零件。模环旋压制程对材料流动,变形和残余应力都有重要影响,对于更好地理解模环旋压过程,提高产品质量和降低生产成本至关重要。因此,本文旨在使用数值模拟方法,研究模环旋压的数值模拟与工艺优化问题。通过对数值模拟结果的分析,优化油压,工件直径和旋转角度等工艺参数。二、数值模拟模型在数值模拟模型中,使
模环旋压成形过程的数值模拟与工艺优化的综述报告.docx
模环旋压成形过程的数值模拟与工艺优化的综述报告模环旋压成形是一种基于金属板材在模圆环内旋转变形的工艺,常用于制造圆环零件,如轴承盖、管道法兰、齿轮、连轴器等。模环旋压成形工艺具有高效、高精度、低成本等优点,因此得到了广泛应用。然而,模环旋压成形过程中存在一些问题,如因模具形状复杂导致成形光顺度差、应力集中等,这些问题直接影响到成形工件的质量。因此,进行模环旋压成形过程的数值模拟与工艺优化,可以提高成形工件的质量和减少生产成本,具有重要的意义。数值模拟是指利用计算机软件对工艺过程进行仿真模拟,以得出工艺参数
模环旋压螺纹管的成形工艺.docx
模环旋压螺纹管的成形工艺模环旋压螺纹管的成形工艺摘要:模环旋压螺纹管是一种常见的管材成形工艺,具有成本低、生产效率高、产品质量好等优点,被广泛应用于各个领域。本文主要介绍了模环旋压螺纹管的成形工艺流程、工艺参数、模具设计及成形工艺中需要注意的问题,旨在深入了解和掌握该工艺的基本原理和操作技巧。1.引言模环旋压螺纹管是一种通过模具的旋转来压制螺纹的成形工艺,该工艺具有成本低、生产效率高、产品质量好等优点,在各个领域得到了广泛应用。本文将围绕模环旋压螺纹管的成形工艺流程、工艺参数、模具设计及成形工艺中需要注意
汽车轮毂旋压成形过程的数值模拟的中期报告.docx
汽车轮毂旋压成形过程的数值模拟的中期报告1.研究背景汽车轮毂是指车轮连接车身的特定部件,它的质量和性能直接影响到汽车的安全性能和行驶稳定性。传统的汽车轮毂制造工艺采用的是压铸和旋压成形。而旋压成形工艺因其造型自由度高、工艺适应性强等优势,近年来得到了越来越广泛的应用。旋压成形过程中,材料在轮毂模具中进行塑性变形,形成轮毂的最终形状。但由于轮毂成形过程中涉及到复杂的力学、热学和物理过程,传统的试验方法难以有效评估轮毂的质量和性能,因此需要采用数值模拟方法进行研究和优化。2.研究内容本研究采用有限元分析方法,
椭圆形封头旋压成形过程数值模拟与分析.docx
椭圆形封头旋压成形过程数值模拟与分析椭圆形封头旋压成形是一种常用于制造容器、油罐和压力器件的成形工艺。它通过将扁平的金属板材放置在特定的模具中,并用旋压机沿着椭圆轨迹施加力量,使板材弯曲成椭圆形,最终形成所需的封头形状。在这个过程中,数值模拟与分析可以发挥重要作用,提供关键的工艺参数和设计指导。首先,数值模拟可以通过有限元分析方法来模拟椭圆形封头旋压成形过程。有限元分析是一种将连续体划分成离散单元,通过建立数学模型和求解有限元方程来分析结构行为的方法。在椭圆形封头旋压成形过程中,有限元分析可用于预测板材的