
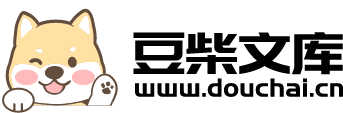
DISA线上生产灰铸铁轮毂类铸件的浇冒口系统及其设计方法.pdf
映雁****魔王
亲,该文档总共16页,到这已经超出免费预览范围,如果喜欢就直接下载吧~
相关资料
DISA线上生产灰铸铁轮毂类铸件的浇冒口系统及其设计方法.pdf
DISA线上生产灰铸铁轮毂类铸件的浇冒口系统及其设计方法,包括冒口和浇注系统,所述浇注系统包括直浇道、内浇道和横浇道,横浇道中垂线的两侧对称设有两个直浇道,每型八个铸件,每个铸件通过相应的内浇道与直浇道相联通,其特征在于八个铸件按照上、中、下分三层布置,且以横浇道中垂线为轴分为左右两侧,左侧上层和中层各布置一个铸件,下层布置两个铸件,右侧上层布置两个铸件,中层和下层各布置一个铸件,每个直浇道均为折线形状,在直浇道的末端设置缓冲区域,内浇道截面形状为矩形,每层直浇道的截面积是位于该层及该层以下内浇道总截面积
精密铸造铸件工艺及浇冒口系统设计.doc
PAGE\*MERGEFORMAT622020年5月29日精密铸造铸件工艺及浇冒口系统设计文档仅供参考铸件工艺设计第一节概述为了生产优质而价廉的包模铸件,做好工艺设计是十分重要的。在做工艺设计之前,首先要考虑选用包模铸造工艺生产时,在质量、工艺和经济方面的几个问题。1.铸件质量的可靠性对于铸件质量上的要求,一般是包括两个方面,一是保证技术要求的尺寸精度、几何精度和表面光洁度,二是保证机械性能和其它工作性能等内在质量方面的要求。包模铸造具有少切削、无切削的突出优点。近年来,由于冶金技术、制模、制壳材料
精密铸造铸件工艺及浇冒口系统设计.docx
编号:时间:2021年x月x日书山有路勤为径,学海无涯苦作舟页码:第页共NUMPAGES33页第PAGE\*MERGEFORMAT33页共NUMPAGES\*MERGEFORMAT33页铸件工艺设计第一节概述为了生产优质而价廉的包模铸件,做好工艺设计是十分重要的。在做工艺设计之前,首先要考虑选用包模铸造工艺生产时,在质量、工艺和经济方面的几个问题。1.铸件质量的可靠性对于铸件质量上的要求,一般是包括两个方面,一是保证技术要求的尺寸精度、几何精度和表面光洁度,二是保证机械
精密铸造铸件工艺及浇冒口系统设计.doc
铸件工艺设计第一节概述为了生产优质而价廉的包模铸件,做好工艺设计是十分重要的。在做工艺设计之前,首先要考虑选用包模铸造工艺生产时,在质量、工艺和经济方面的几个问题。1.铸件质量的可靠性对于铸件质量上的要求,一般是包括两个方面,一是保证技术要求的尺寸精度、几何精度和表面光洁度,二是保证机械性能和其它工作性能等内在质量方面的要求。包模铸造具有少切削、无切削的突出优点。近年来,由于冶金技术、制模、制壳材料和工艺以及检测技术等方面的发展,包模铸件的外部和内在质量不断提高,所以它的应用范围愈来愈广。不少锻件、焊接件
精密铸造铸件工艺及浇冒口系统设计.docx
编号:时间:2021年x月x日书山有路勤为径学海无涯苦作舟页码:铸件工艺设计第一节概述为了生产优质而价廉的包模铸件做好工艺设计是十分重要的。在做工艺设计之前首先要考虑选用包模铸造工艺生产时在质量、工艺和经济方面的几个问题。1.铸件质量的可靠性对于铸件质量上的要求一般是包括两个方面一是保证技术要求的尺寸精度、几何精度和表面光洁度二是保证机械性能和其它工作性能等内在质量方面的要求。包模铸造具有少切削、无切削的突出优点。近年来