
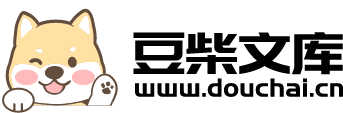
一种考虑多部位及多失效模式的涡轮盘损伤容限评估方法.pdf
一吃****福乾
亲,该文档总共24页,到这已经超出免费预览范围,如果喜欢就直接下载吧~
相关资料
一种考虑多部位及多失效模式的涡轮盘损伤容限评估方法.pdf
本发明涉及一种考虑多部位及多失效模式的涡轮盘损伤容限评估方法,步骤:(1)获取涡轮盘工况条件,包括载荷谱,典型温度等;(2)确立三种典型失效模式:盘心低循环疲劳失效、盘缘蠕变\疲劳失效、榫接结构高低周复合疲劳失效;(3)针对三种失效模式,分别开展宏微观裂纹扩展实验,采集材料裂纹扩展性能数据;(4)建立描述涡轮盘材料低循环疲劳、蠕变\疲劳、高低周复合疲劳典型失效模式的裂纹扩展寿命预测方法,形成考虑多部位及多失效模式的涡轮盘损伤容限评估方法。
涡轮盘偏心孔部位制造缺陷损伤容限分析.docx
涡轮盘偏心孔部位制造缺陷损伤容限分析摘要涡轮盘是一种用于提高发动机性能和效率的关键部件,在其制造过程中存在一定的缺陷损伤,如偏心孔、裂纹等。本文通过分析涡轮盘的相关资料,研究了涡轮盘偏心孔部位制造缺陷损伤容限分析。采用有限元分析法对涡轮盘偏心孔部位进行模拟分析,并对损伤容限进行了预测和探讨,结果表明偏心孔处缺陷对涡轮盘的损伤容限存在影响。通过本文的研究,有助于提高涡轮盘的制造质量和安全性能。关键词:涡轮盘;偏心孔;缺陷损伤容限;有限元分析引言涡轮盘是现代发动机中重要的动力部件之一,其作用是通过压缩进气机吸
涡轮盘的损伤容限分析.docx
涡轮盘的损伤容限分析涡轮盘的损伤容限分析引言:涡轮盘是一种广泛应用于航空、航天、能源等领域的旋转机械部件。在运行过程中,涡轮盘由于受到高温、高压、高速等工况的影响,容易发生损伤。因此,进行涡轮盘的损伤容限分析,对于提高涡轮盘的可靠性和寿命具有重要意义。一、涡轮盘的损伤类型及原因分析涡轮盘的损伤主要包括疲劳裂纹、应力腐蚀裂纹、高温熔解、热胀冷缩等。这些损伤主要由以下原因引起:首先,涡轮盘在高温和高压环境下运行,会引起材料的退火、晶粒长大和氧化等,导致材料的力学性能下降,从而造成损伤。其次,涡轮盘在高速旋转时
一种考虑过渡过程的轮盘概率失效风险评估用应力分区方法.pdf
本发明公开了一种考虑过渡过程的轮盘概率失效风险评估用应力分区方法,属于风险评估领域。首先通过有限元分析获得发动机轮盘在飞行循环中的随时间变化的应力分布,建立量化的分区准则,对轮盘进行初始分区,获得若干预分区。然后根据过渡过程中每一个预分区内单元随时间变化的轮盘应力,若预分区内的应力梯度超出给定阈值,将该预分区细分为不少于两个的子分区,且子分区满足分区准则,保证各个预分区在整个飞行循环内均满足分区阈值的要求。针对应力梯度满足给定阈值的各个预分区,分别分析每一个预分区的失效概率,最终汇总得到轮盘的总失效风险。
一种多失效模式融合机电作动器健康状态评估方法.pdf
本发明适用于机电作动器故障诊断领域,提供了一种多失效模式融合机电作动器健康状态评估方法。由于EMA的健康状态受到多种失效模式及其耦合因素共同作用,使得EMA的综合健康状态不仅受到单个失效模式和多个失效模式叠加影响,还受到多失效模式之间的耦合因素影响,导致多失效模式耦合下健康状态评估模型无法真实反映综合健康状态问题。因此,本发明提出一种多失效模式耦合下多模型概率迁移融合机制,深入分析多失效模式之间耦合因素对于模型融合过程的影响机理,构建了面向多健康状态评估模型融合交互逻辑,建立了可以刻画多失效模式耦合因素影